Mould making is a complex process that requires a combination of advanced design, selection of high-quality materials, innovative technology and strict quality control.
From automotive parts to medical devices or consumer goods, the quality of a mould directly impacts the precision, functionality, and durability of the final product.
1. DFM (Design for Manufacturability)
The use of comprehensive DFM reports allows for the optimization of design and the streamlining of production. These reports provide critical information about potential challenges and manufacturing limitations, enabling efficient redesigns. With the application of DFM, parts are designed to minimize waste and enhance the overall quality of the final product. DFM makes the whole process simpler and more effective.
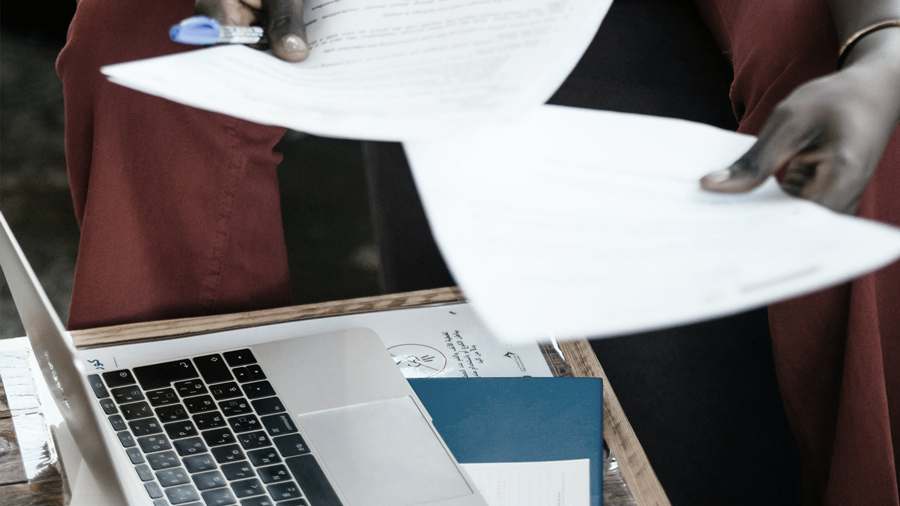
2. Design and Precision Engineering
The foundation of any successful mould lies in its design. Using computer-aided design (CAD) software makes it possible to create intricate 3D models with micrometric precision. Every aspect, from the mould’s geometry to its complex cooling channels, is meticulously planned and optimized to ensure flawless performance. Precision engineering guarantees that all technical specifications are defined, with strict GD&T principles, minimizing the margin for error and maximizing the mould’s functionality.
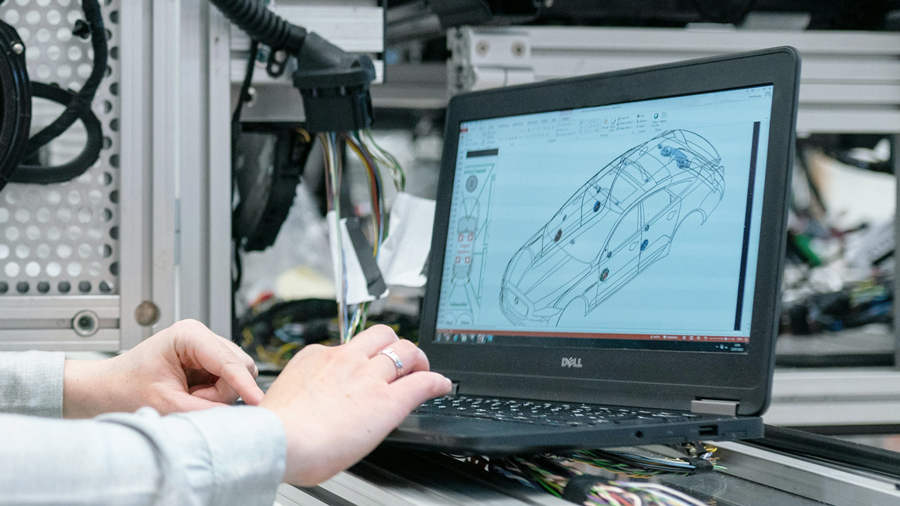
3. High-performance materials
The selection of appropriate materials is crucial to the durability and performance of the mould. Materials such as high-strength steels, special alloys and coatings, are often used due to their wear resistance and ability to withstand the demanding conditions of injection moulding processes. The correct choice of materials ensures that the mould can withstand extreme pressures, temperatures and cyclical loads without compromising its integrity or the quality of the end product.
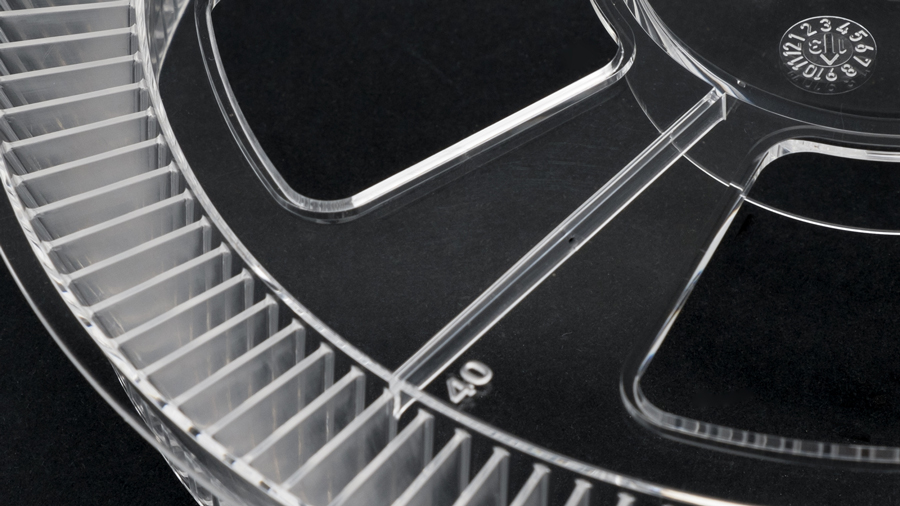
4. Innovative production technology
Advanced technologies such as precision CNC machining and 3D printing enable the production of moulds with micrometric accuracy, significantly reducing delivery times and, therefore, reducing costs. This micrometric precision guarantees a significant decrease of future bench work, consequently minimizing the human error factor and maximizing consistency. Automation also plays a crucial role, as it ensures consistent quality, timings and opens up for a more accurate project planning.
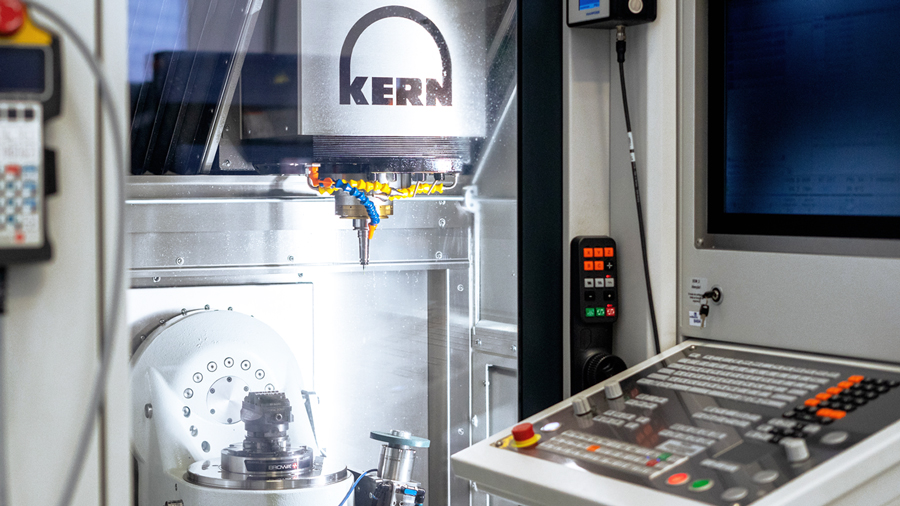
5. Strict quality control
At various stages of the production process, extensive visual inspection and metrology are carried out to identify and correct any defects or imperfections. This includes dimensional checking and 3D surface analysis, ensuring that the final mould complies with all technical specifications.
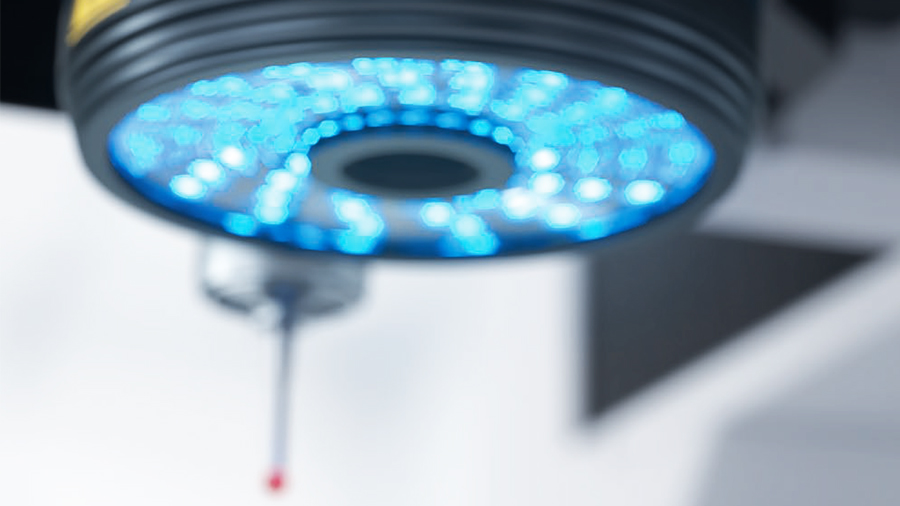
Ensuring Excellence in Mould Manufacturing
Manufacturing high-quality moulds depends on an integrated approach that combines detailed design, robust materials, advanced technology and meticulous quality control. These five key factors are vital to ensure that the moulds produced are durable, precise and capable of meeting the requirements of customers and industrial applications.