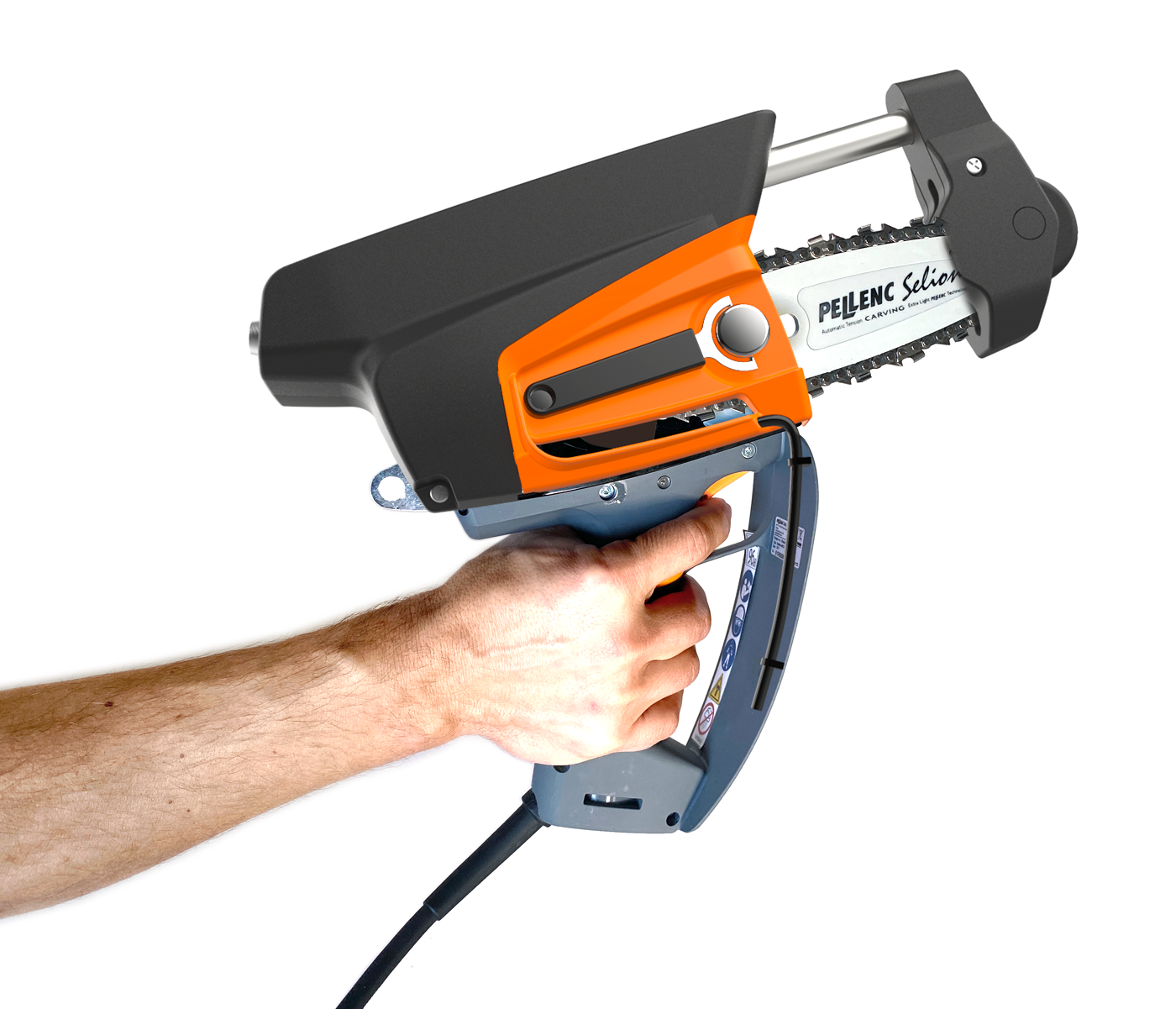
Case Study
Cork Harvesting
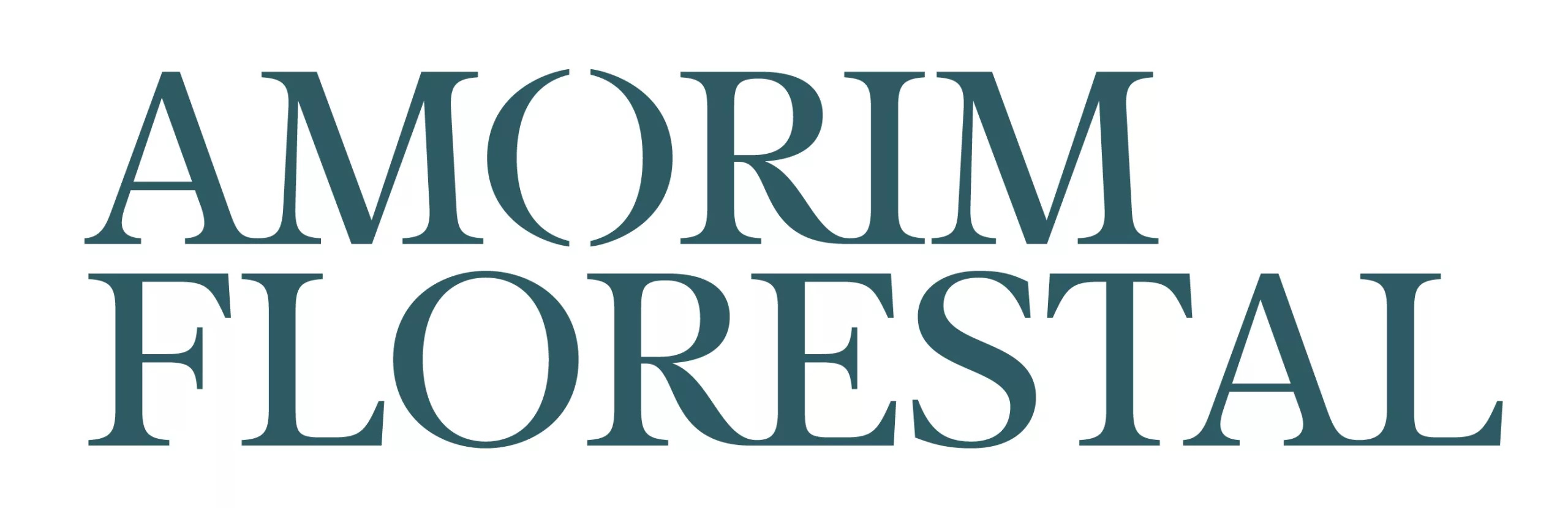
A challenge from the world’s largest cork processing group, Corticeira Amorim, has resulted in an innovative device.
In partnership with AMORIM, our Design, Prototyping & Rapid Manufacturing Unit has developed a machine capable of simplifying the work of cork harvesters and preserving cork oaks, combining creative engineering with functionality.
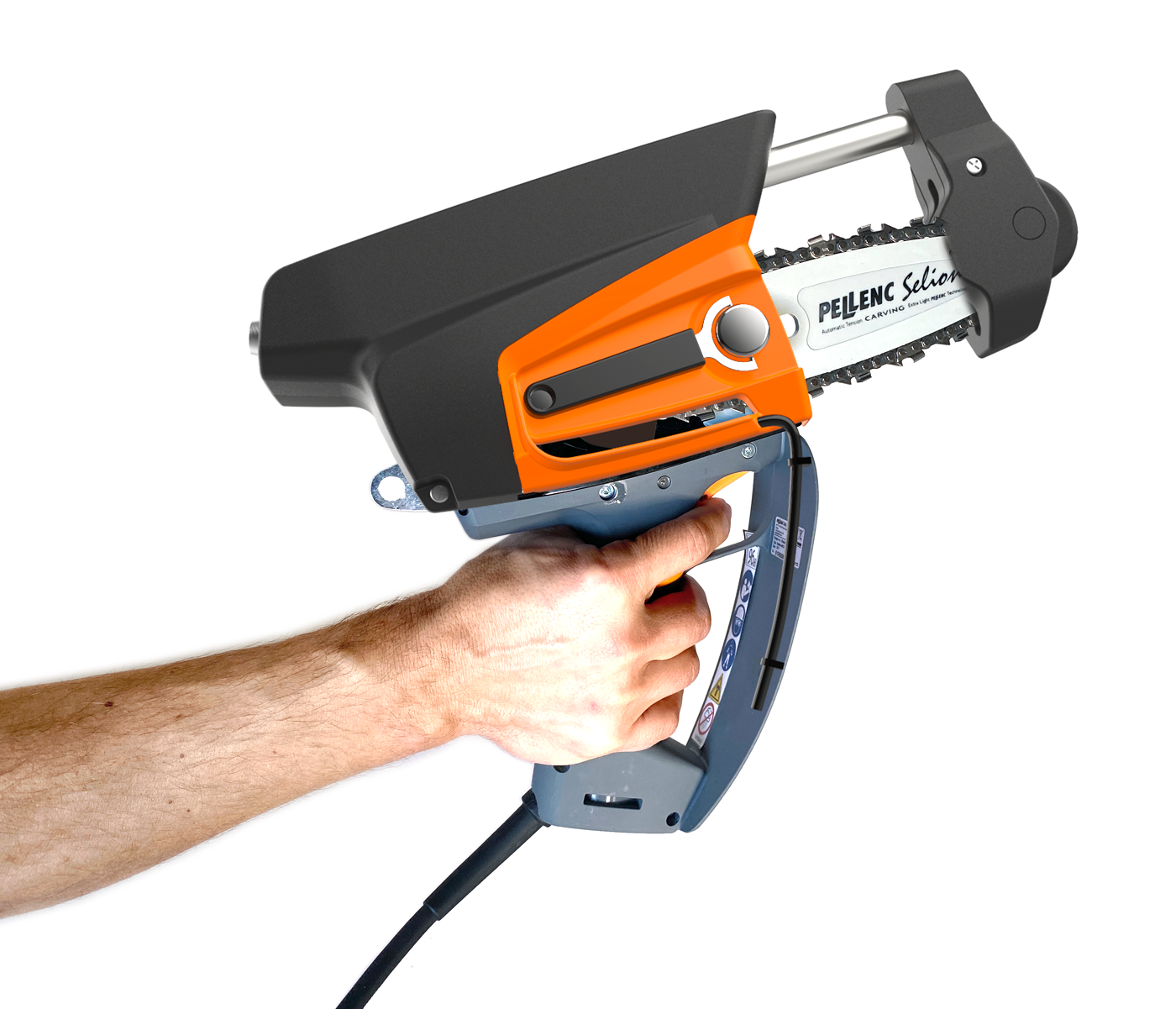
Case Study
Cork Harvesting
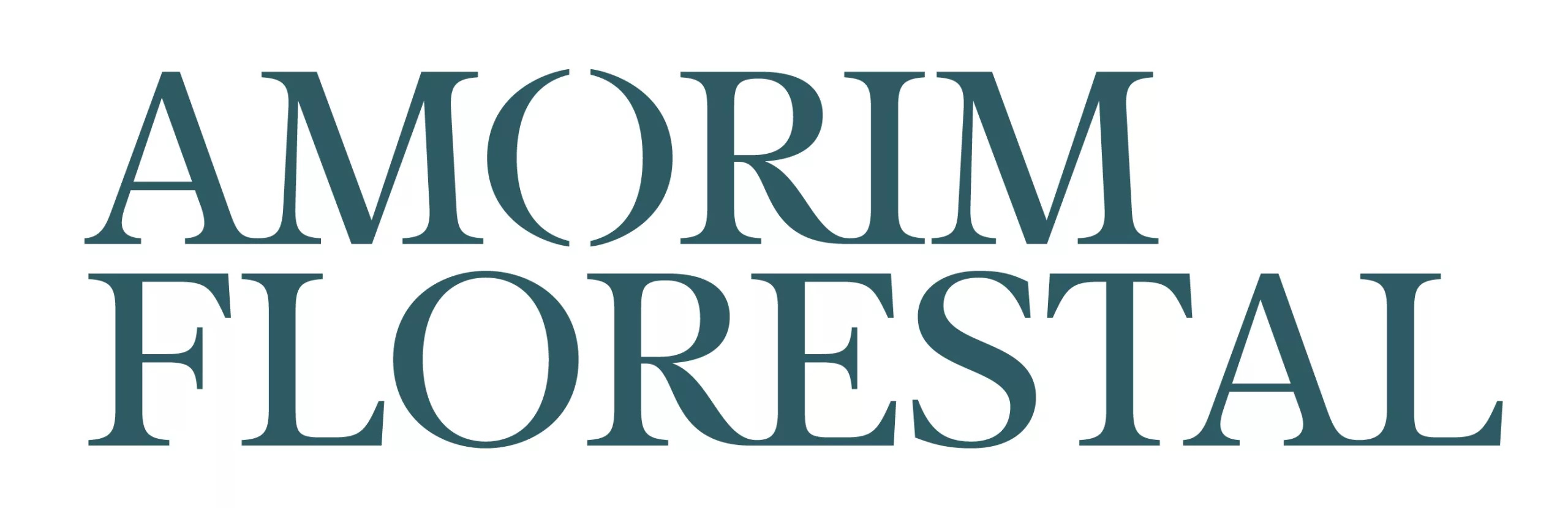
A challenge from the world’s largest cork processing group, Corticeira Amorim, has resulted in an innovative device.
In partnership with AMORIM, our Design, Prototyping & Rapid Manufacturing Unit has developed a machine capable of simplifying the work of cork harvesters and preserving cork oaks, combining creative engineering with functionality.
Traditional Cork Harvesting: A Challenge
The traditional extraction process involves expertise. Skilled workers are required to extract cork from trees, traditionally using axes. However, they must avoid touching the tree trunk, as this can negatively impact or even prevent cork growth in subsequent years. Faced with this issue, AMORIM identified the need to develop a device that would allow extraction without harming the trees, catering even to less experienced operators and cork harvesters resistant to change.
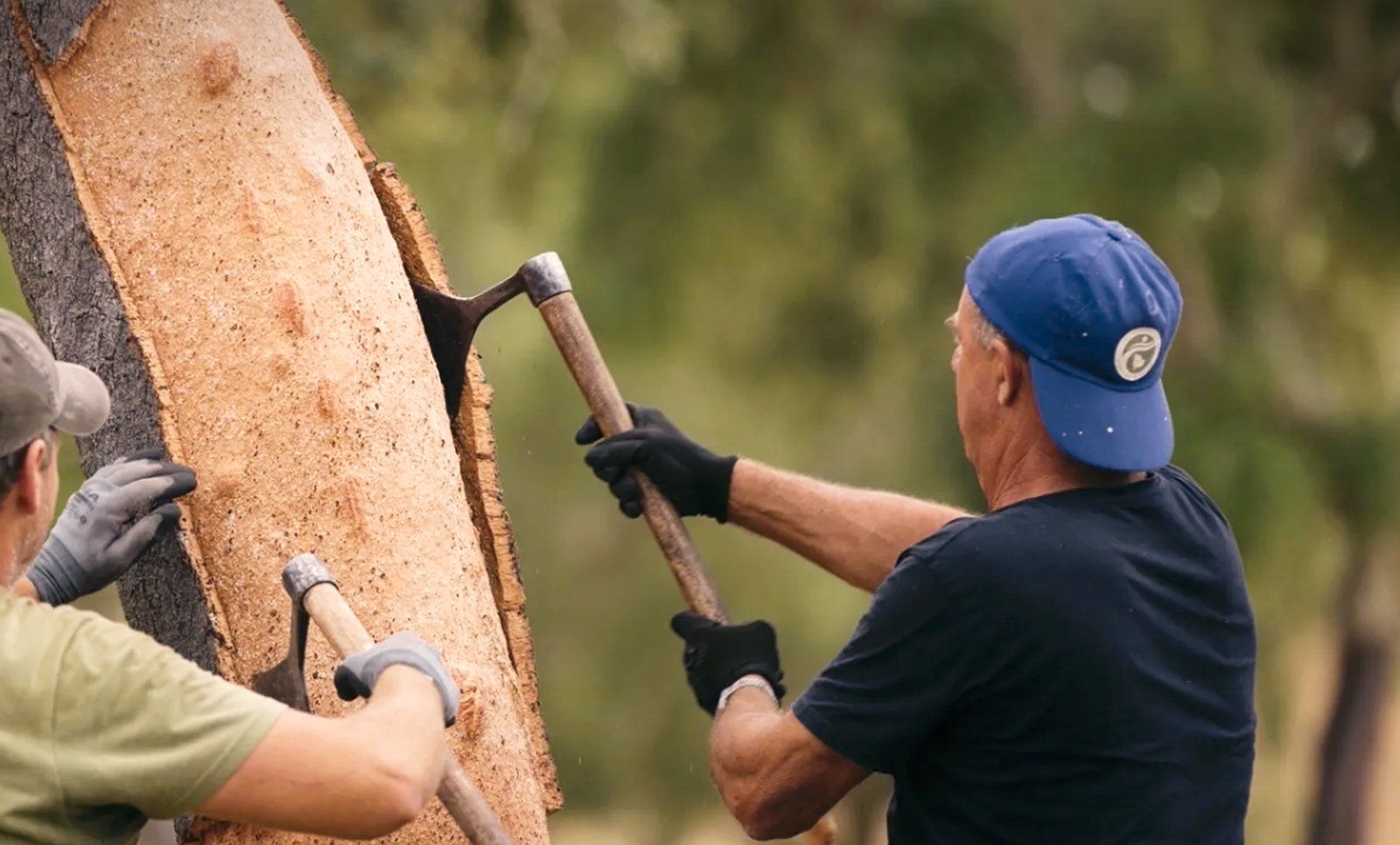
Photo ©Amorim
1. Creating a new product from existing equipment
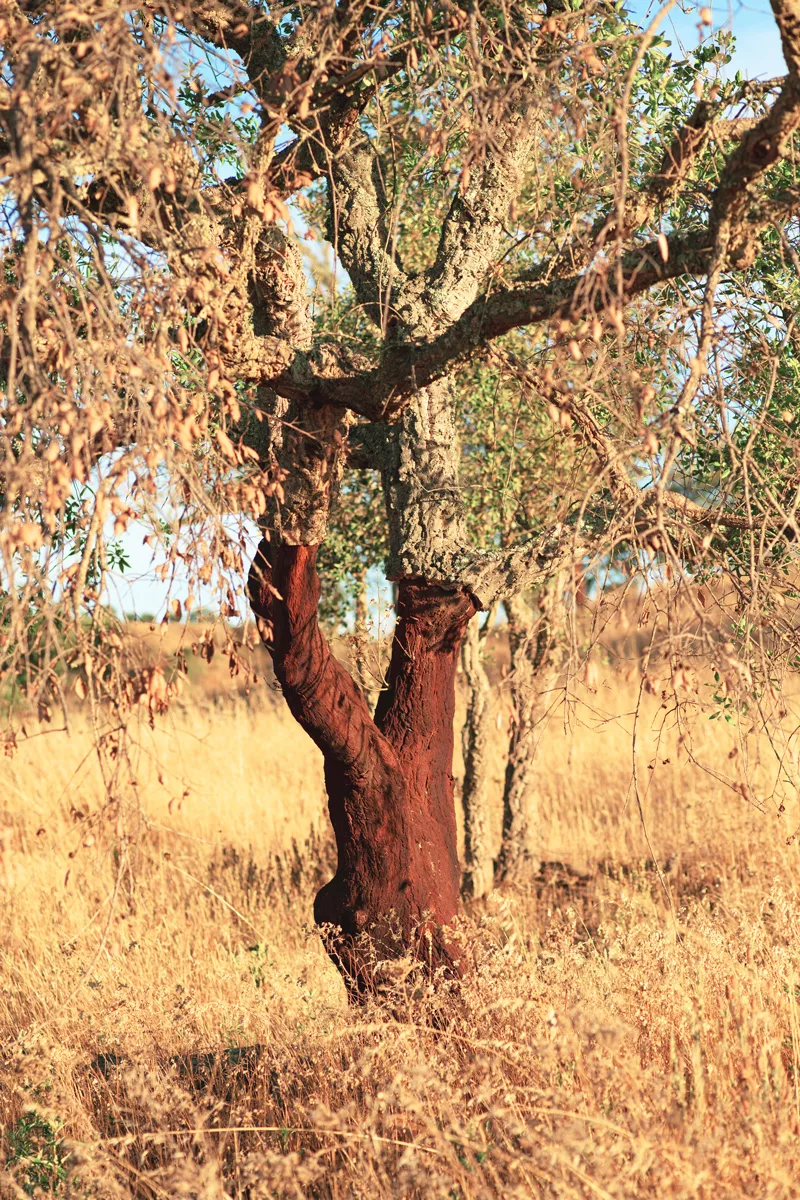
As the project progressed, we improved the product’s usability, facilitating its integration for users less receptive to change. Today we have a machine that is light and easy to use, with an aesthetic that conveys quality and confidence.
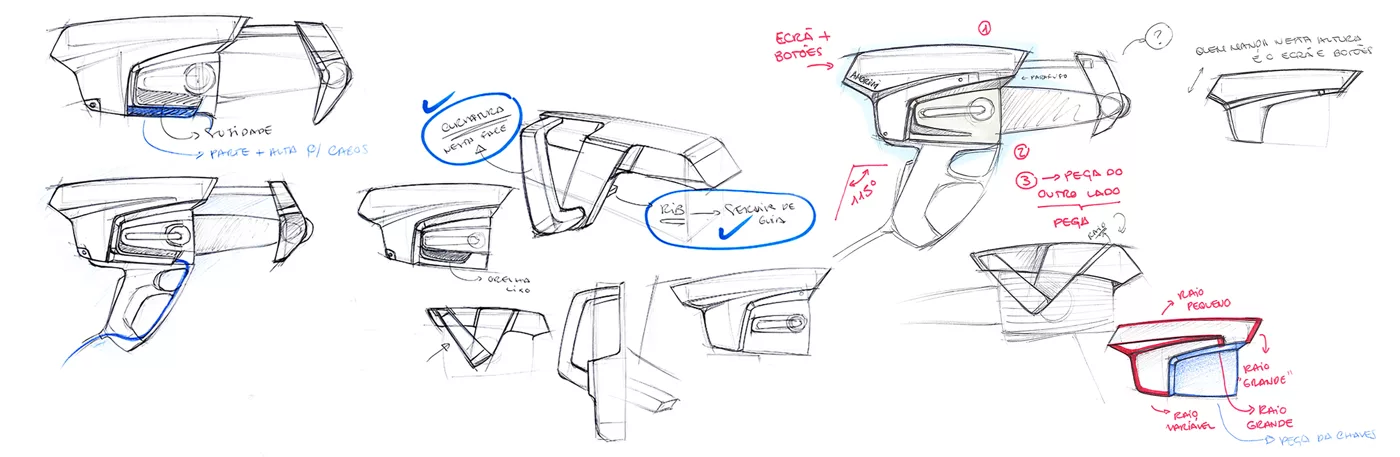
2. Design Engineering
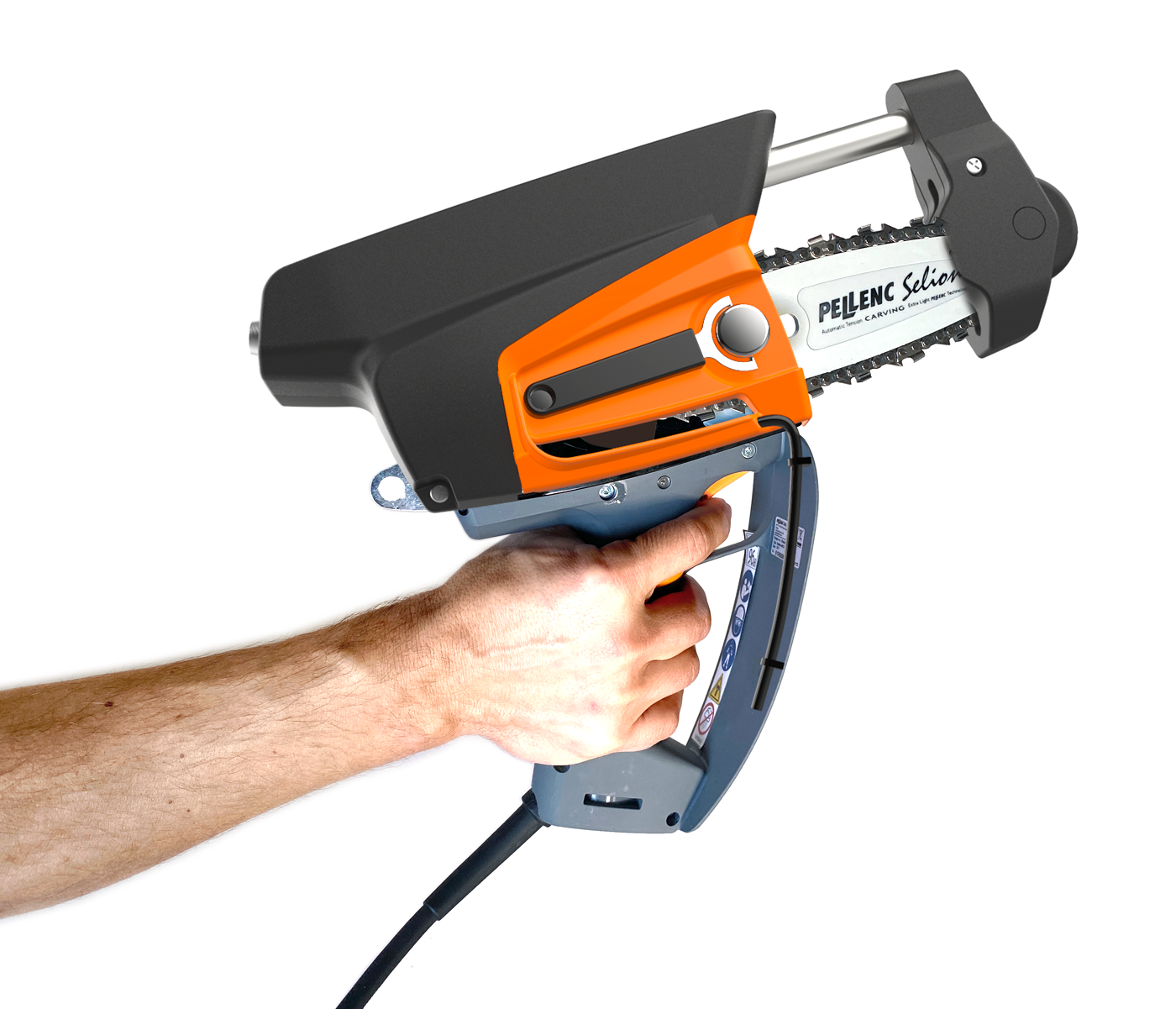
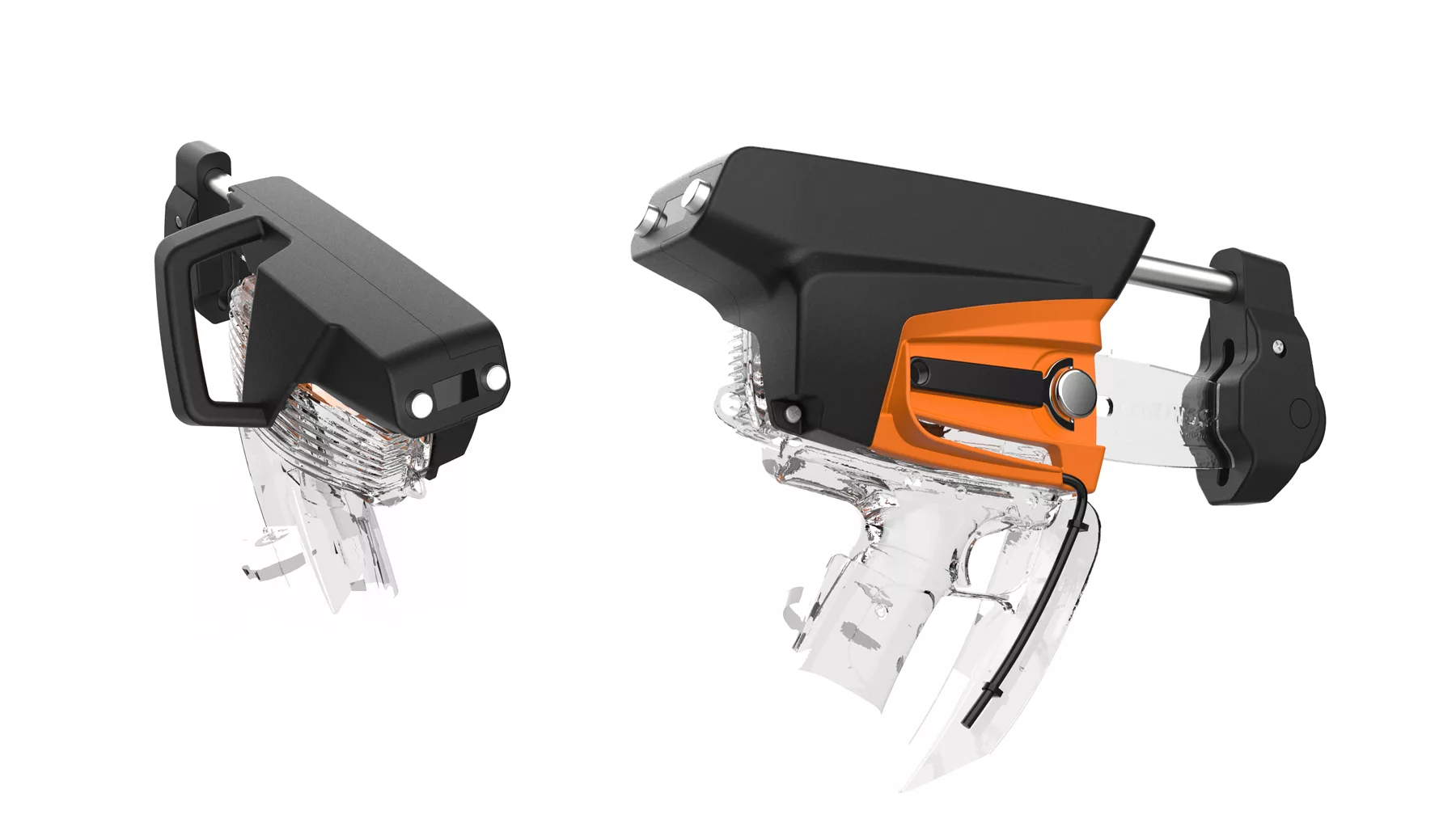
Faced with the challenge to preserve access to raw materials while safeguarding the cork regeneration cycle, AMORIM sought a partner capable of providing expertise in creative engineering, along with the ability to develop an impactful product, thereby easing its integration with users resistant to change.
They found this ally in GRANDESIGN, our business unit specializing Design, Prototyping & Rapid Manufacturing. The diverse production techniques offered by GRANDESIGN proved to be a significant advantage, as they ensured the ability to explore multiple solutions.
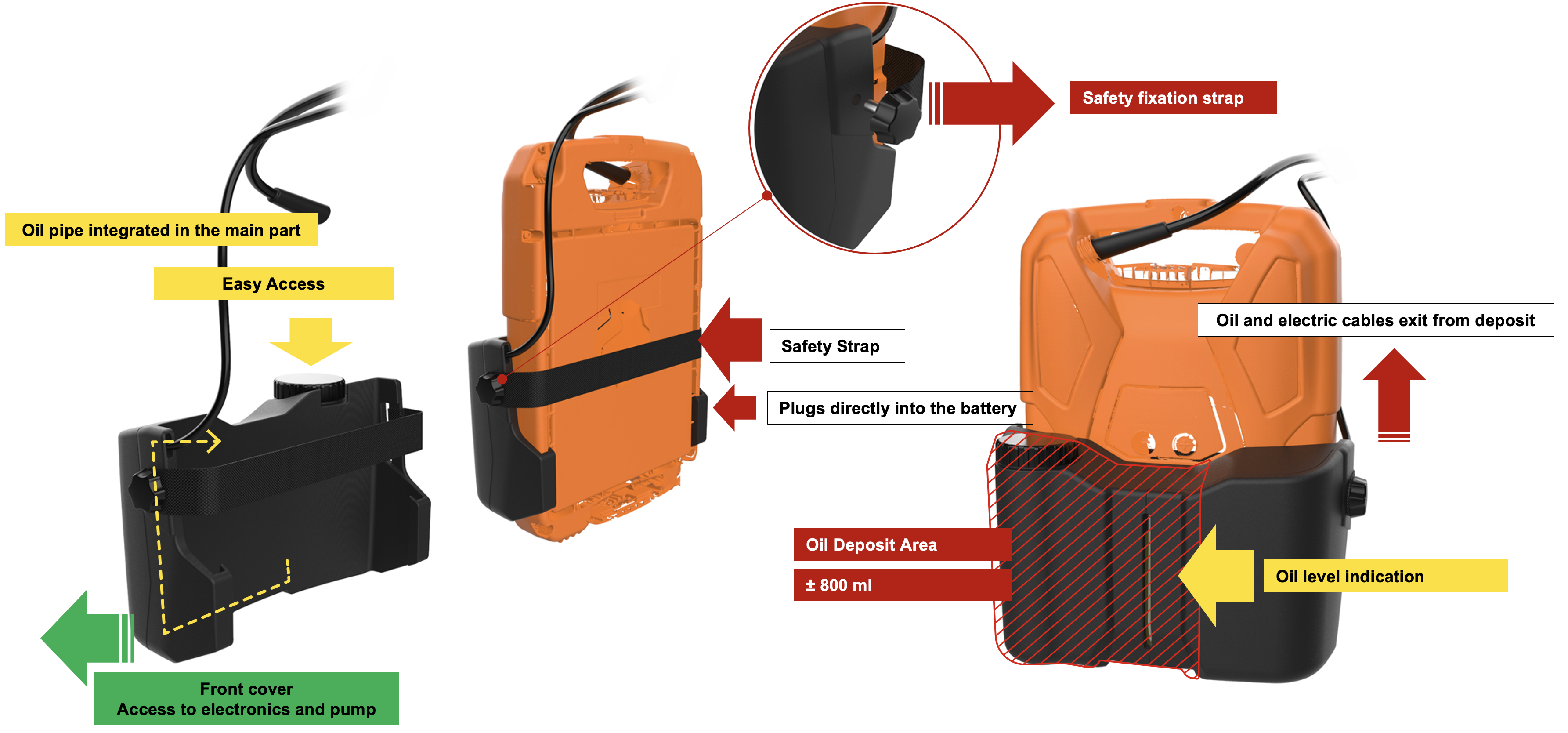
3. Prototyping and Validation
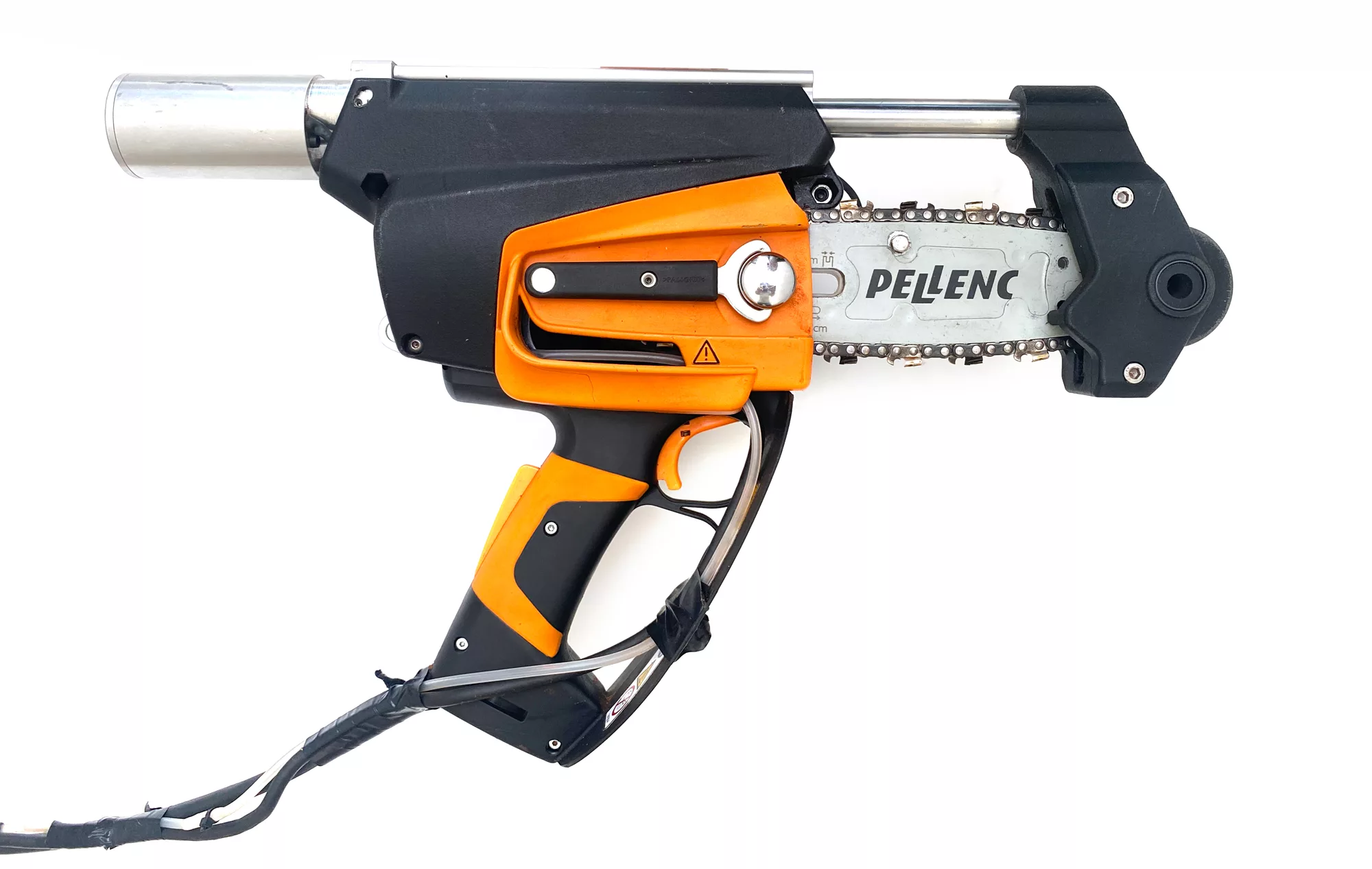
Harvesting for cork trees
We used rapid prototyping techniques to produce five initial prototypes, capable of withstanding the effort and rough handling associated with the tasks. Maintaining a focus on the project’s future, the GRANDESIGN team designed and painted the new parts to seamlessly integrate with the base machine, forming a cohesive unit. To ensure a robust assembly between the different components, small aluminum plates were used to create strong joints.
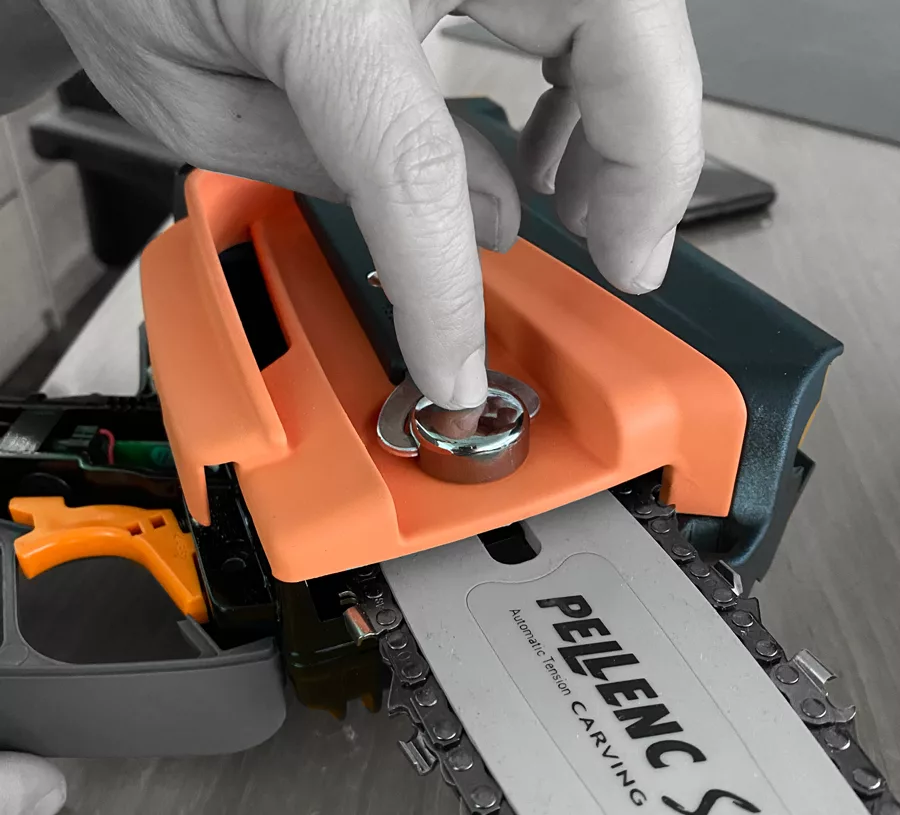
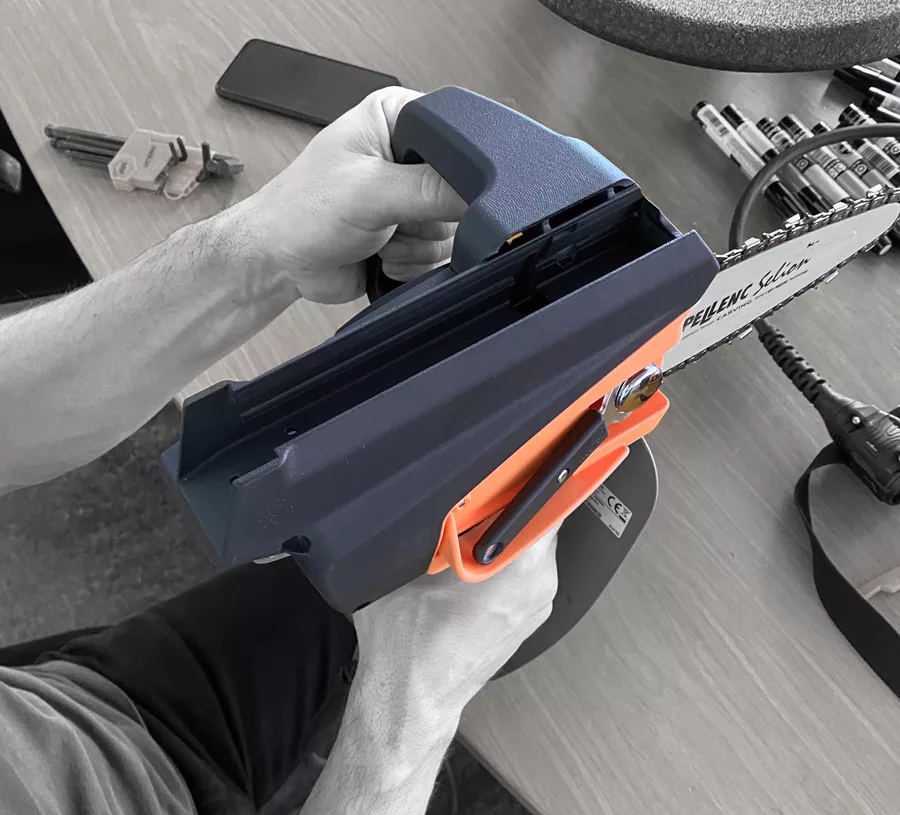
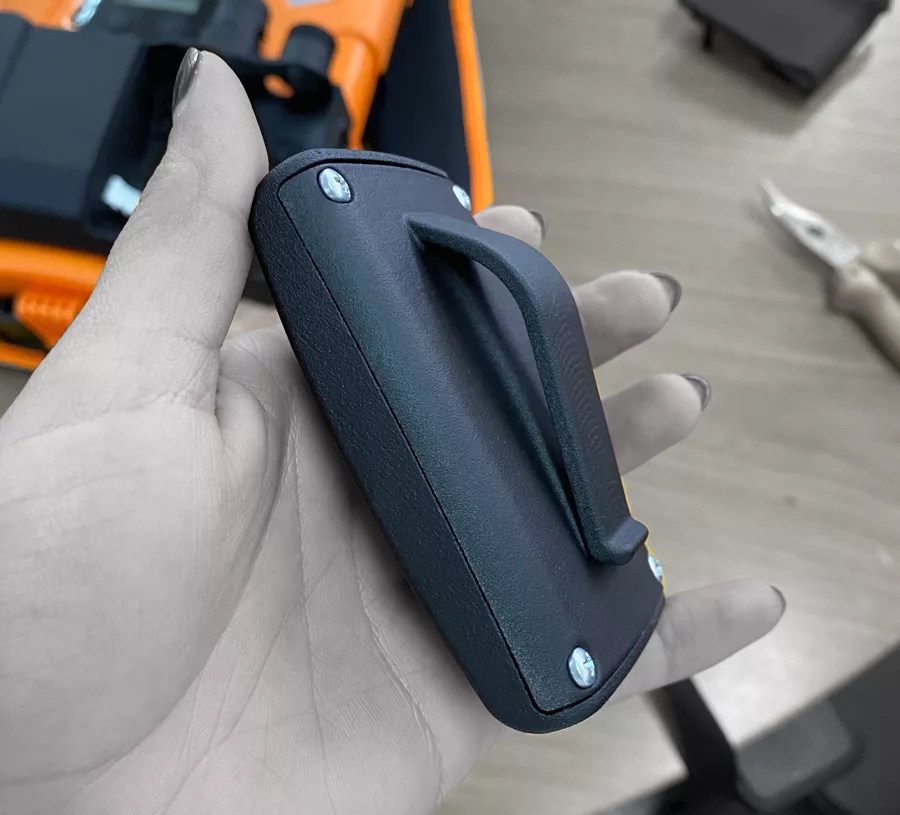
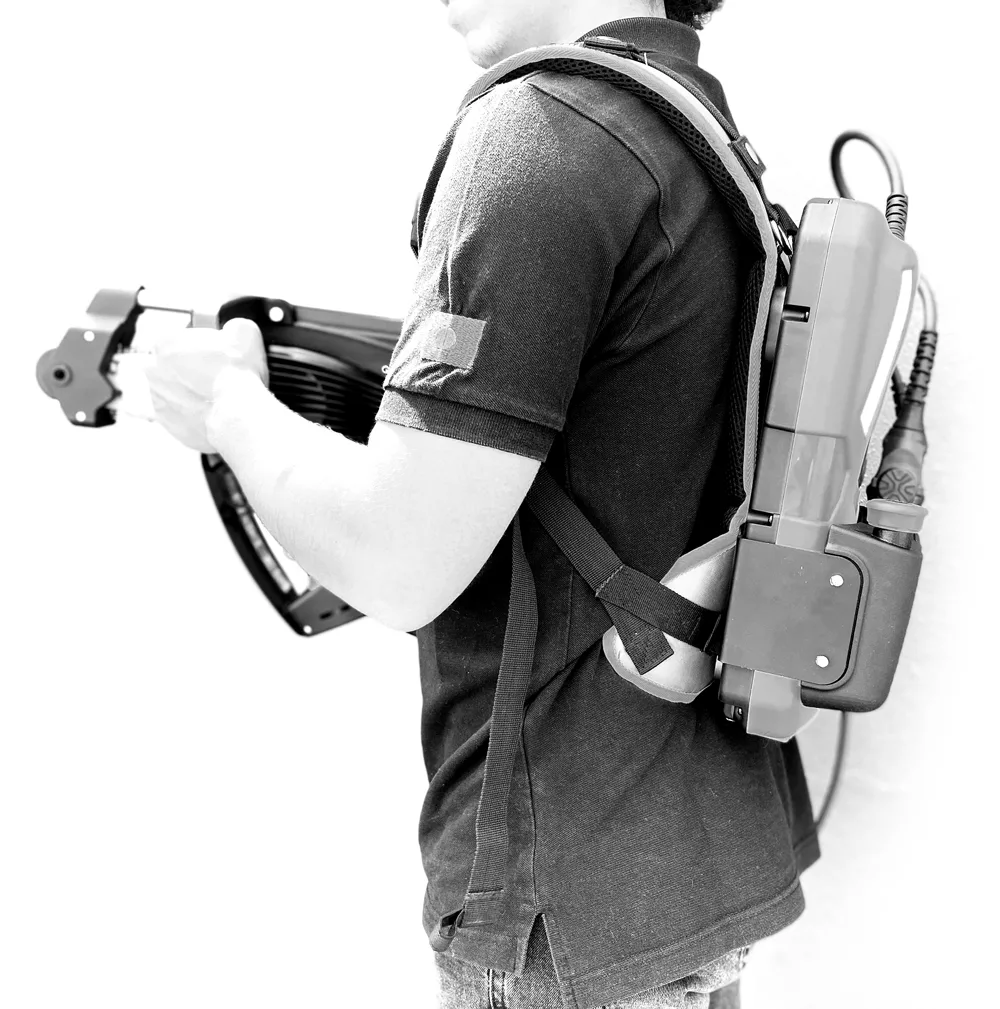
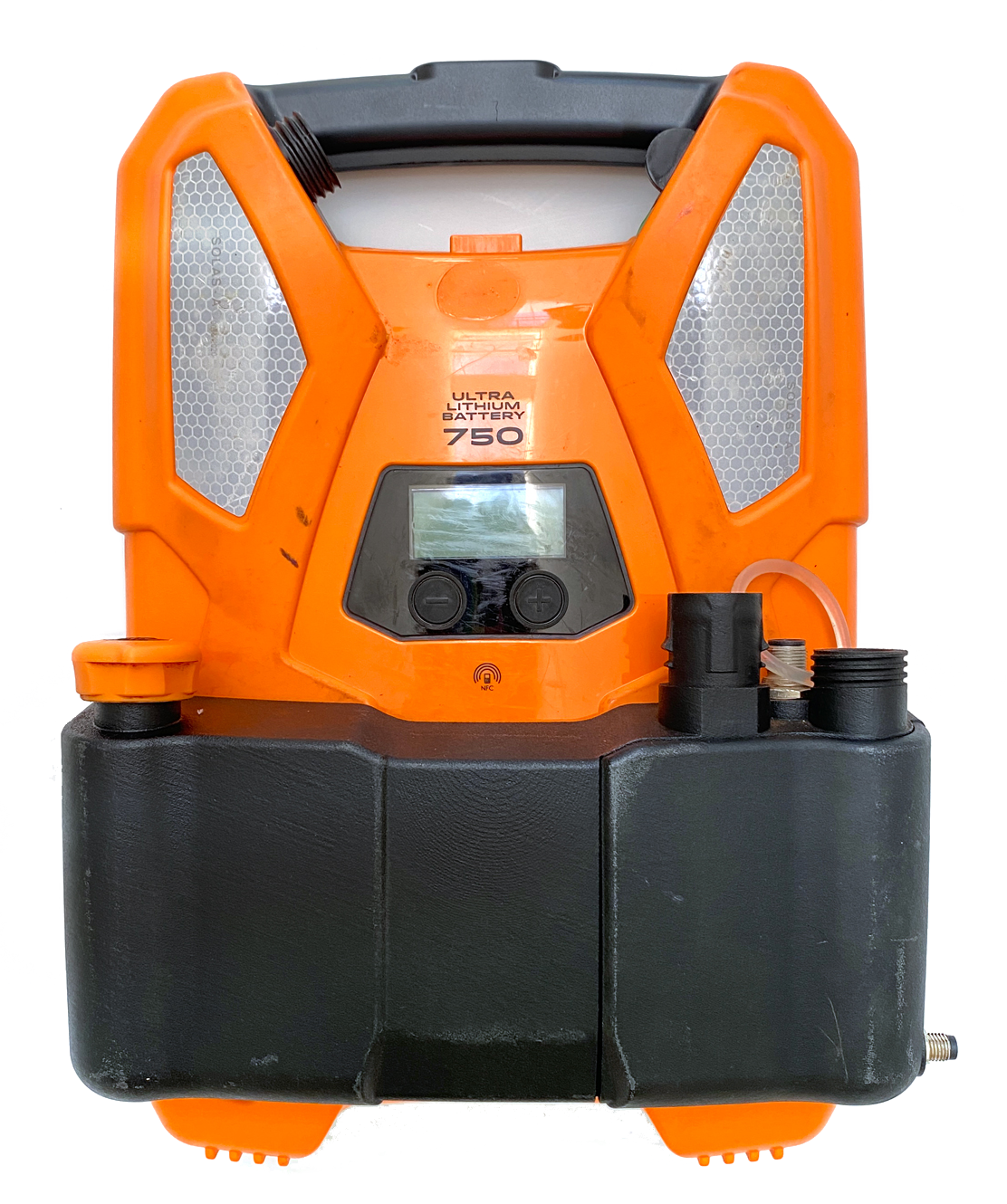
Battery + Oil Deposit
4. Small Series Manufacturing
We conducted tests using the machine in real-world conditions, and some fine-tuning corrections were made. The results were very positive, leading to the advancement of serial production. For the 2024 production, improvements were implemented and applied in a small production run, maintaining the same processes and retaining 95% of the original machine.
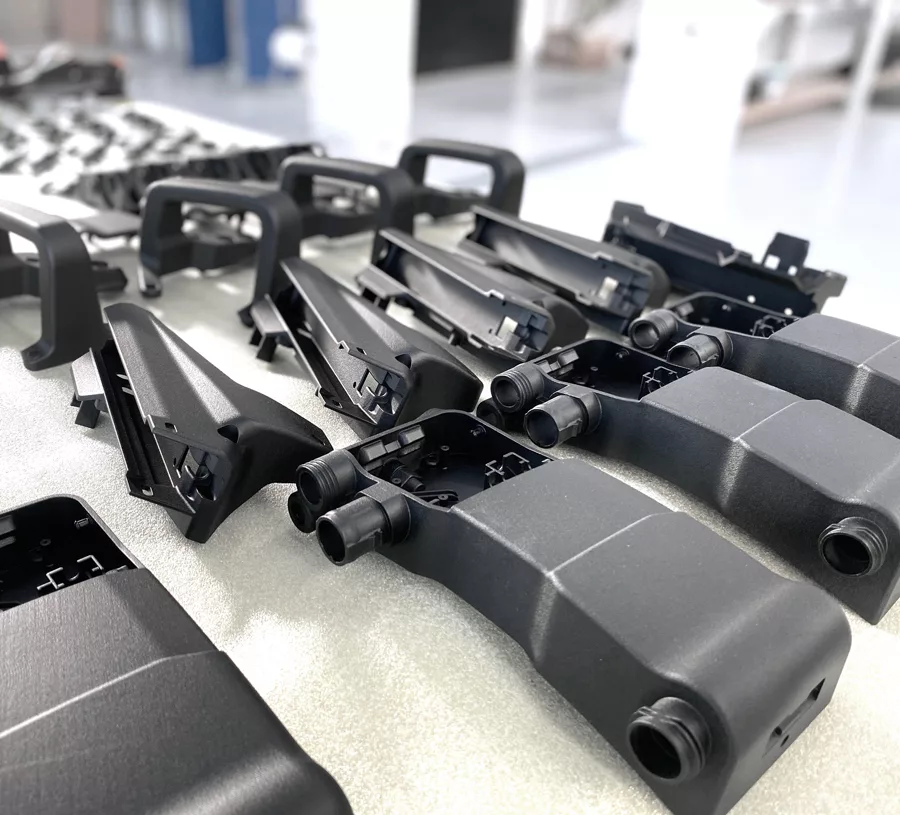
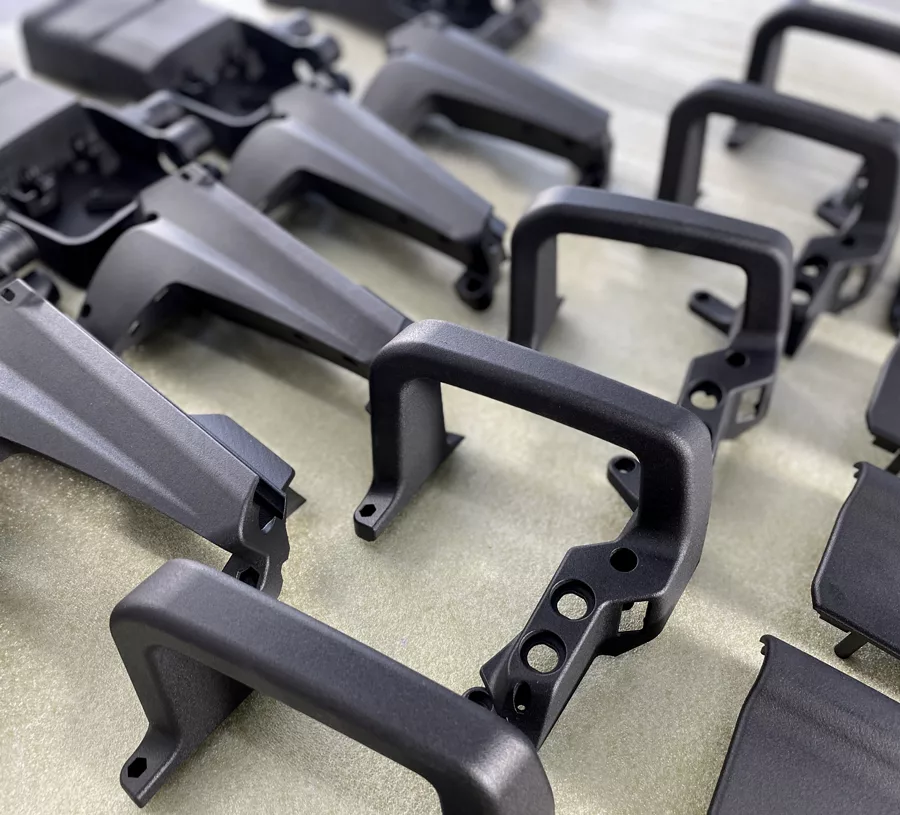
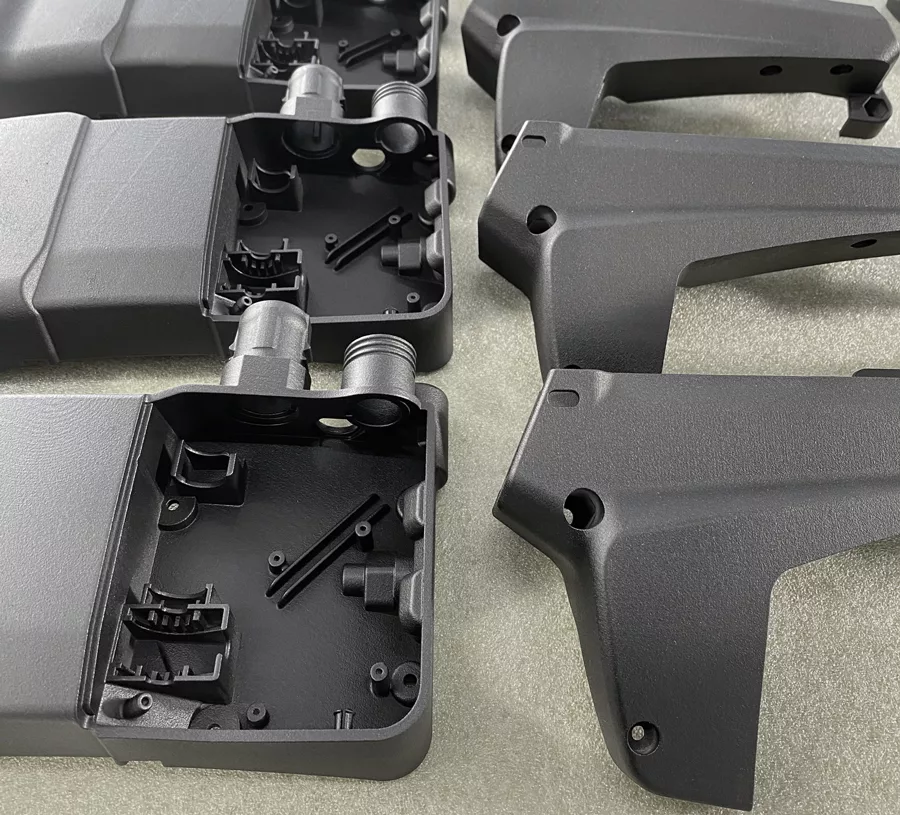
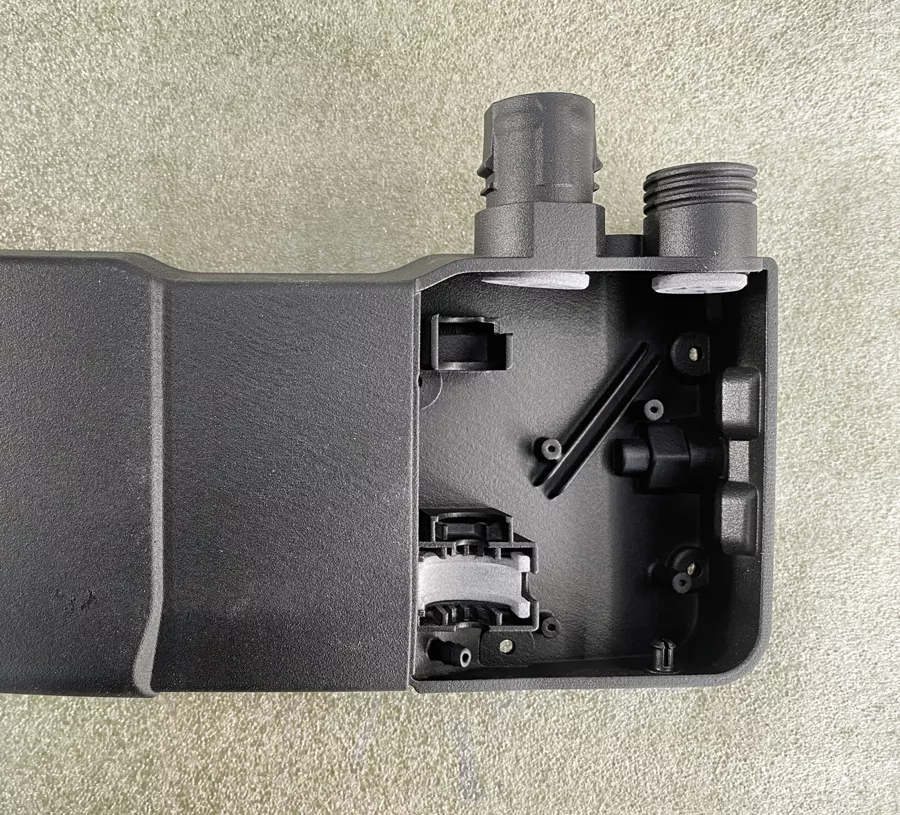
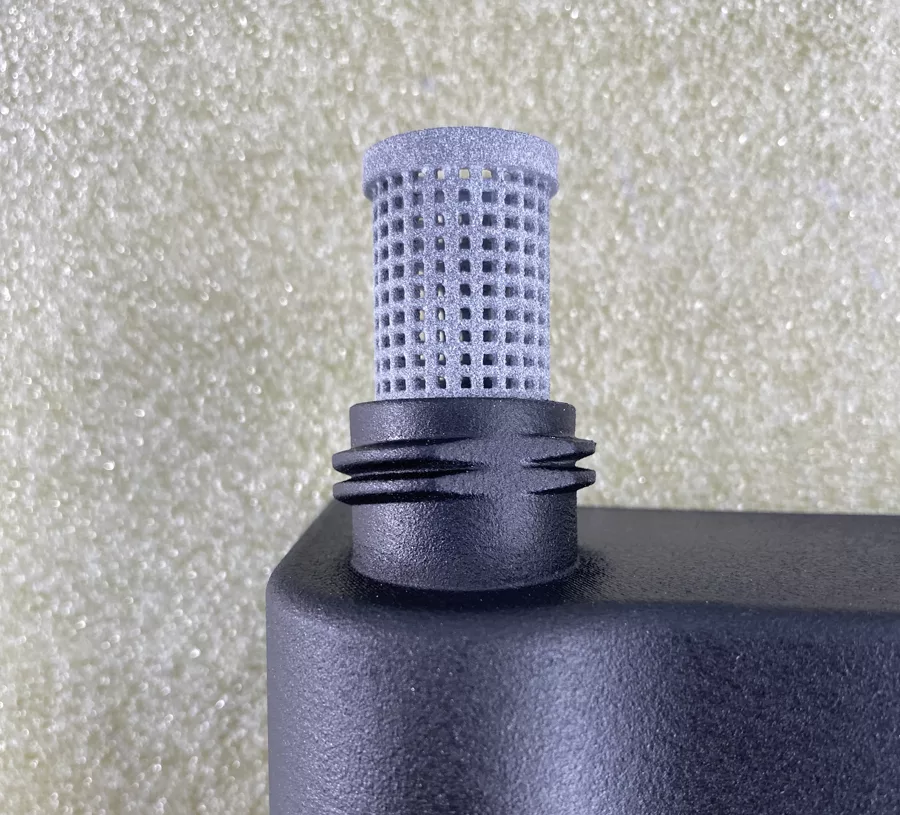
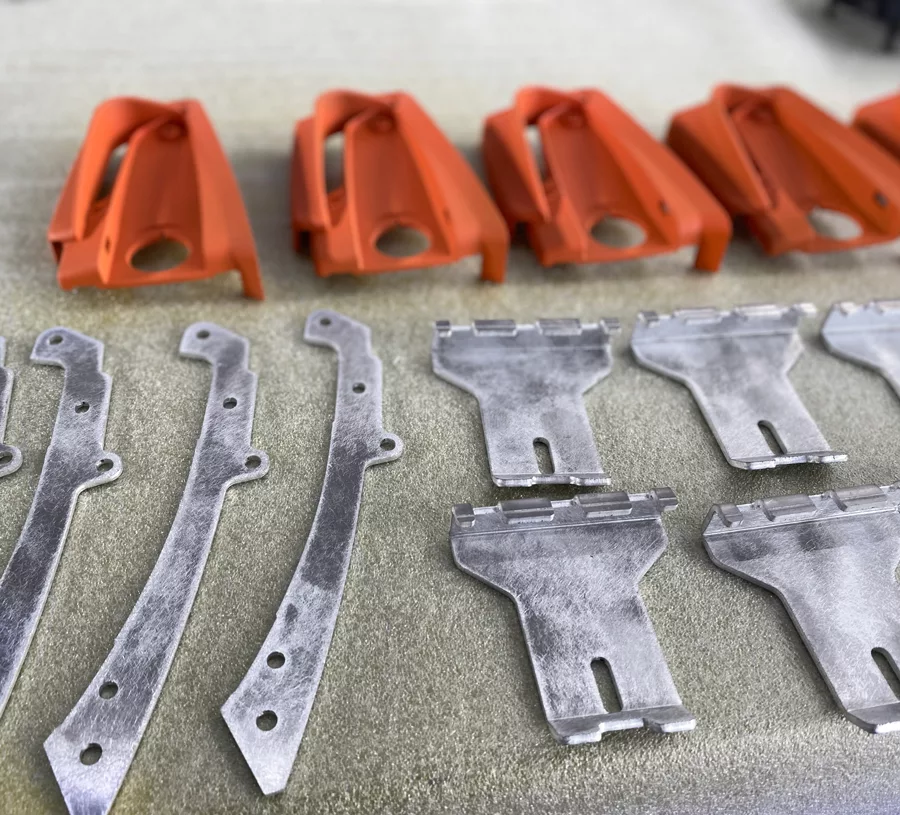
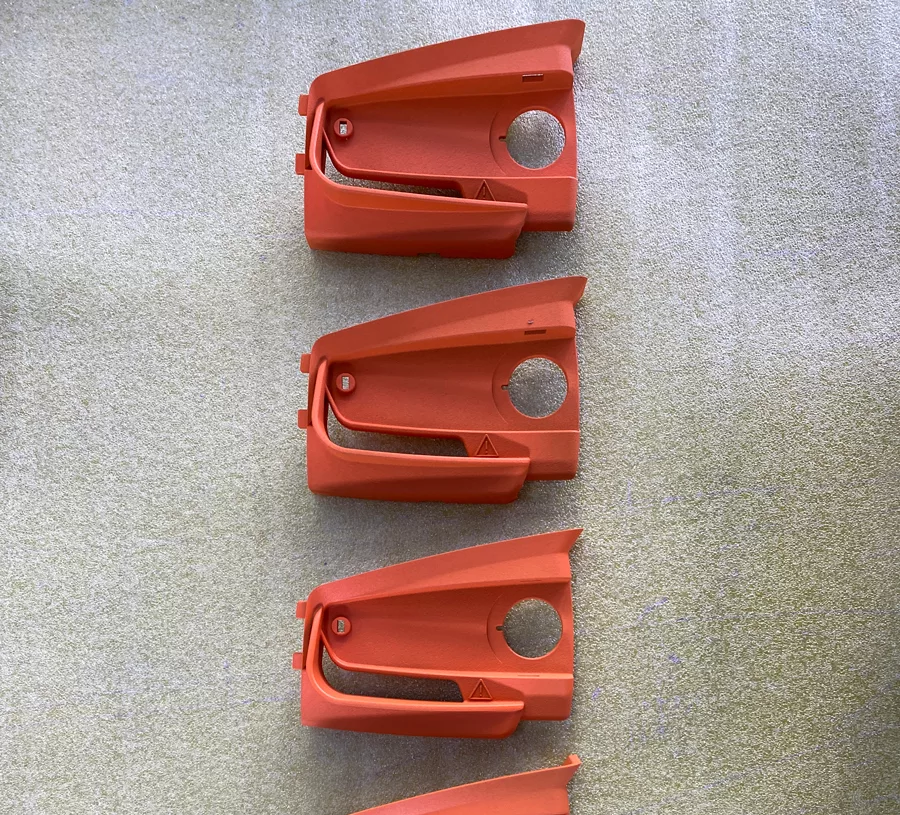
Through a collaborative, client-centric approach, we refined a device that not only addresses the specific needs of tree preservation but also enhances the efficiency of cork harvesters’ work.
Innovation, efficiency and sustainability
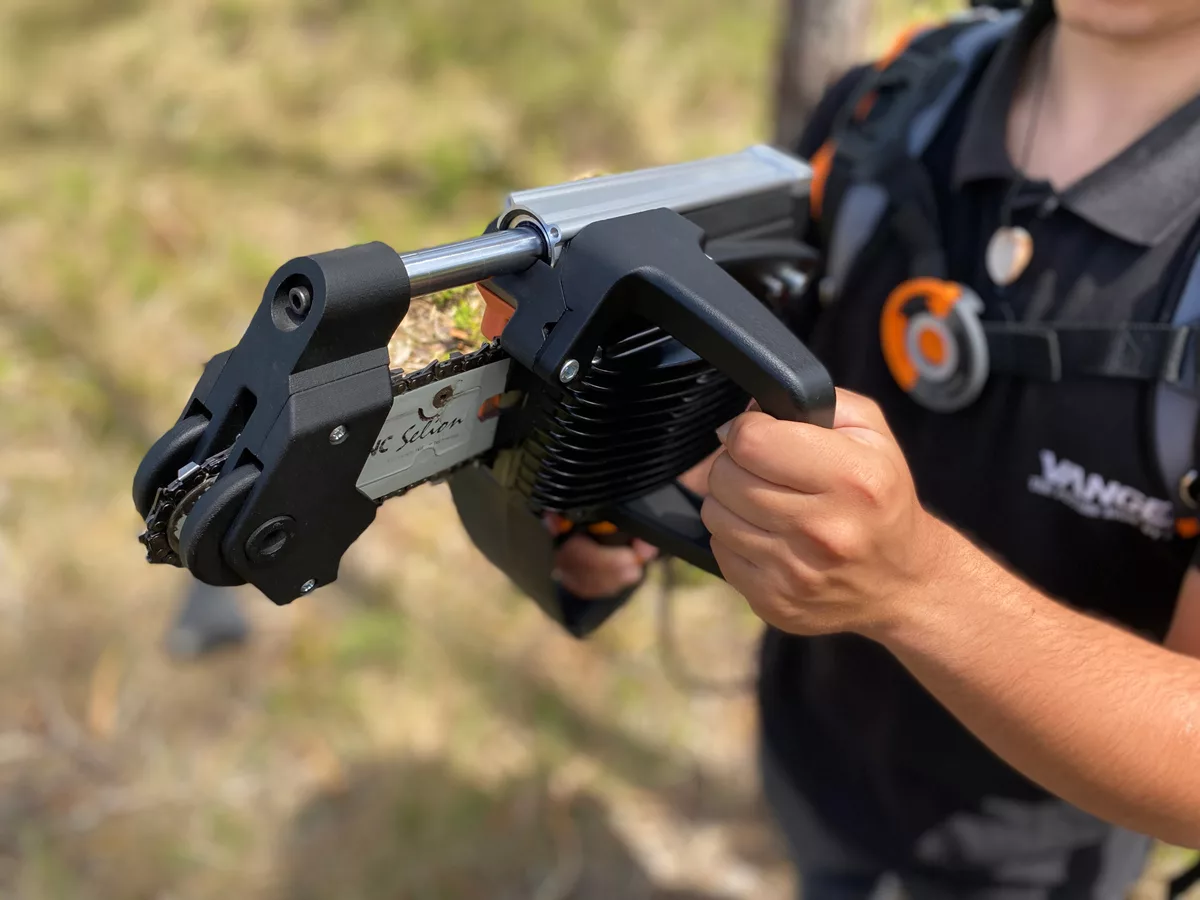
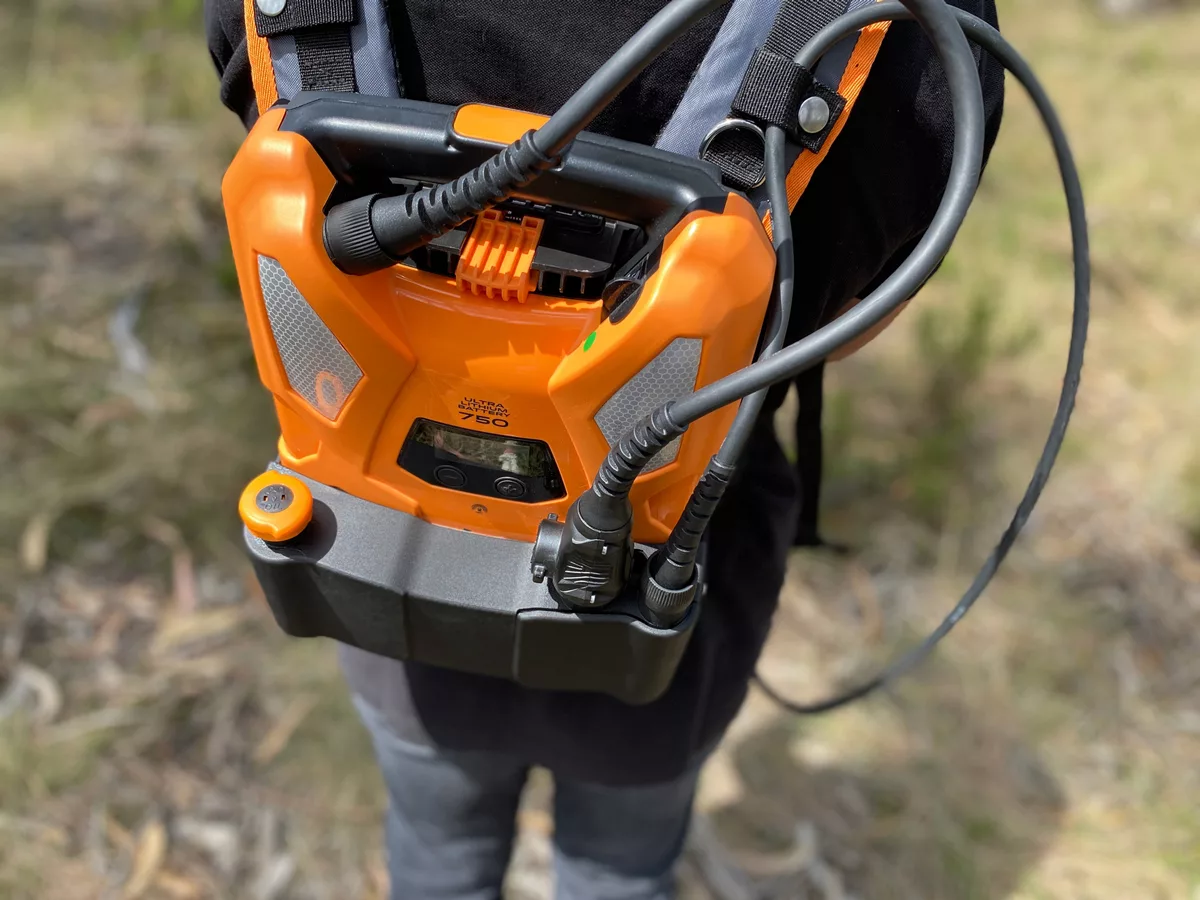
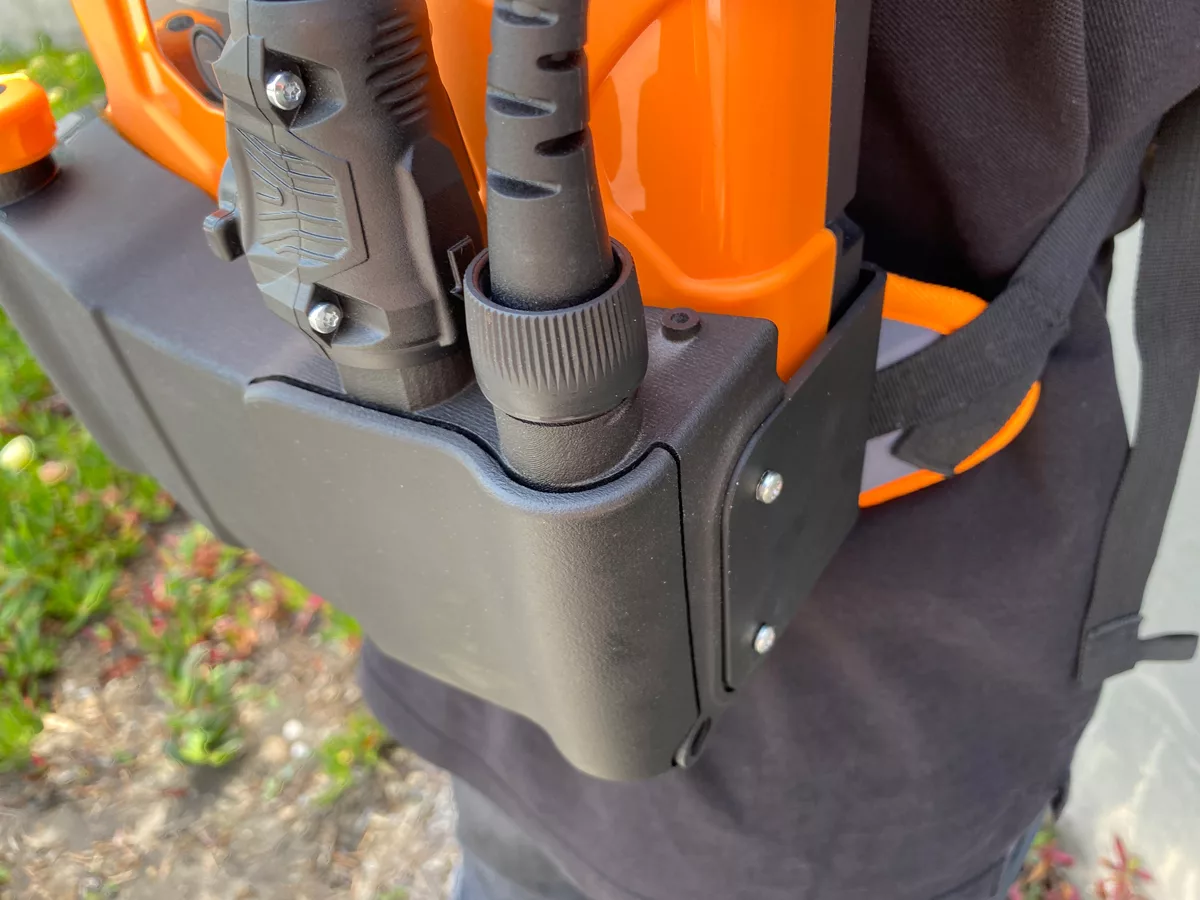
Video ©Amorim
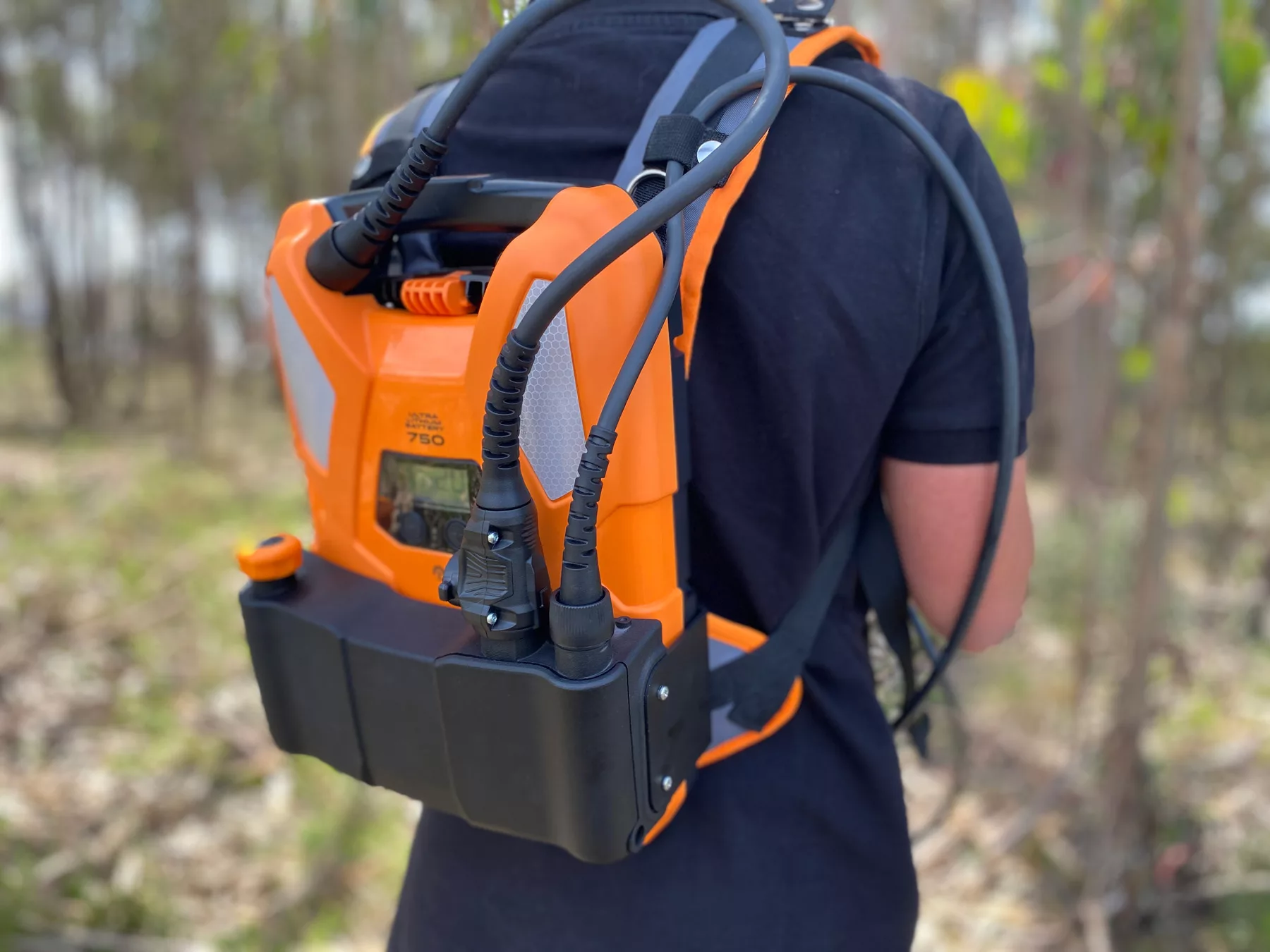
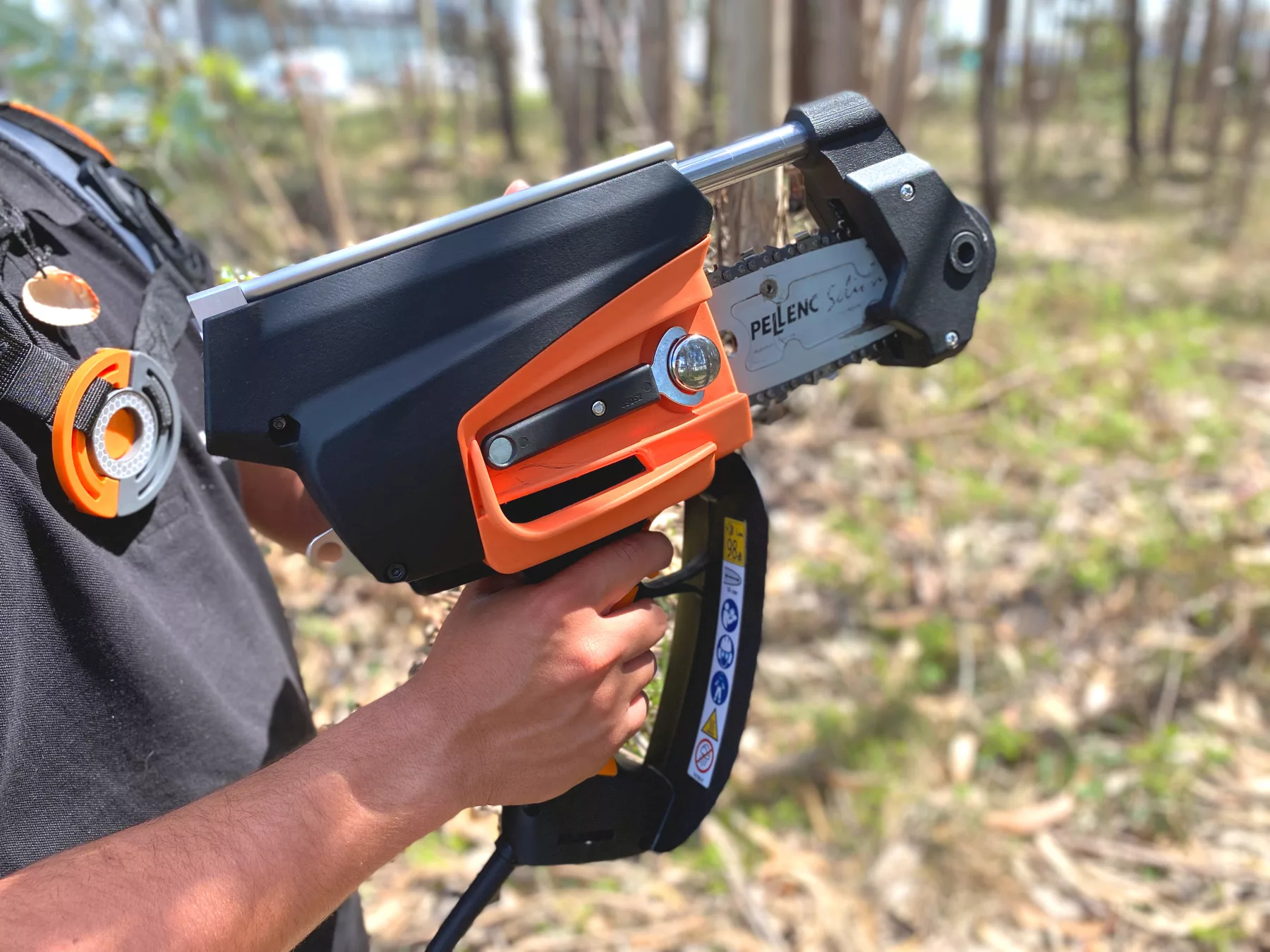
Innovation, efficiency and sustainability
Through a collaborative, client-centric approach, we refined a device that not only addresses the specific needs of tree preservation but also enhances the efficiency of cork harvesters’ work.
Video ©Amorim
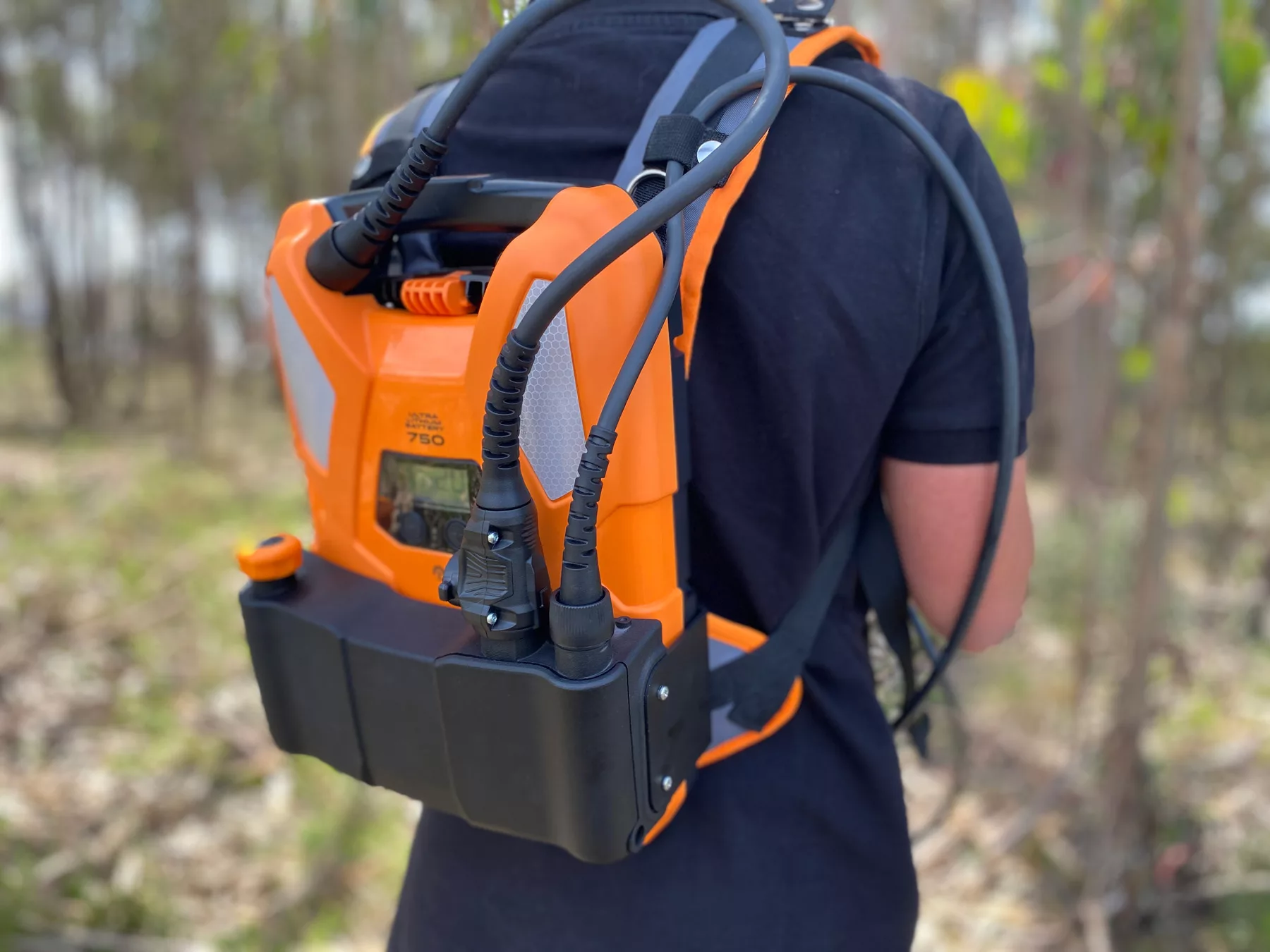
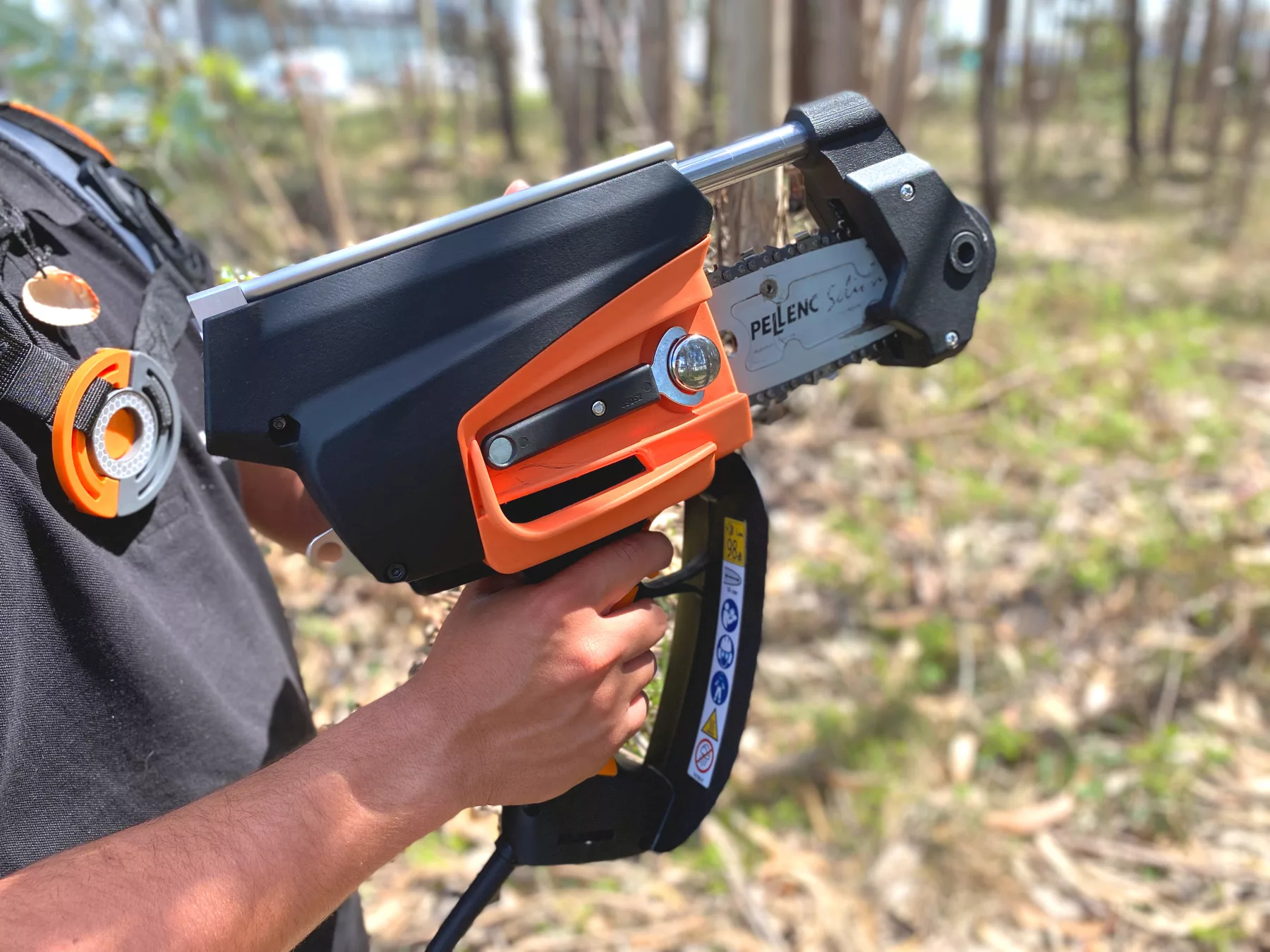
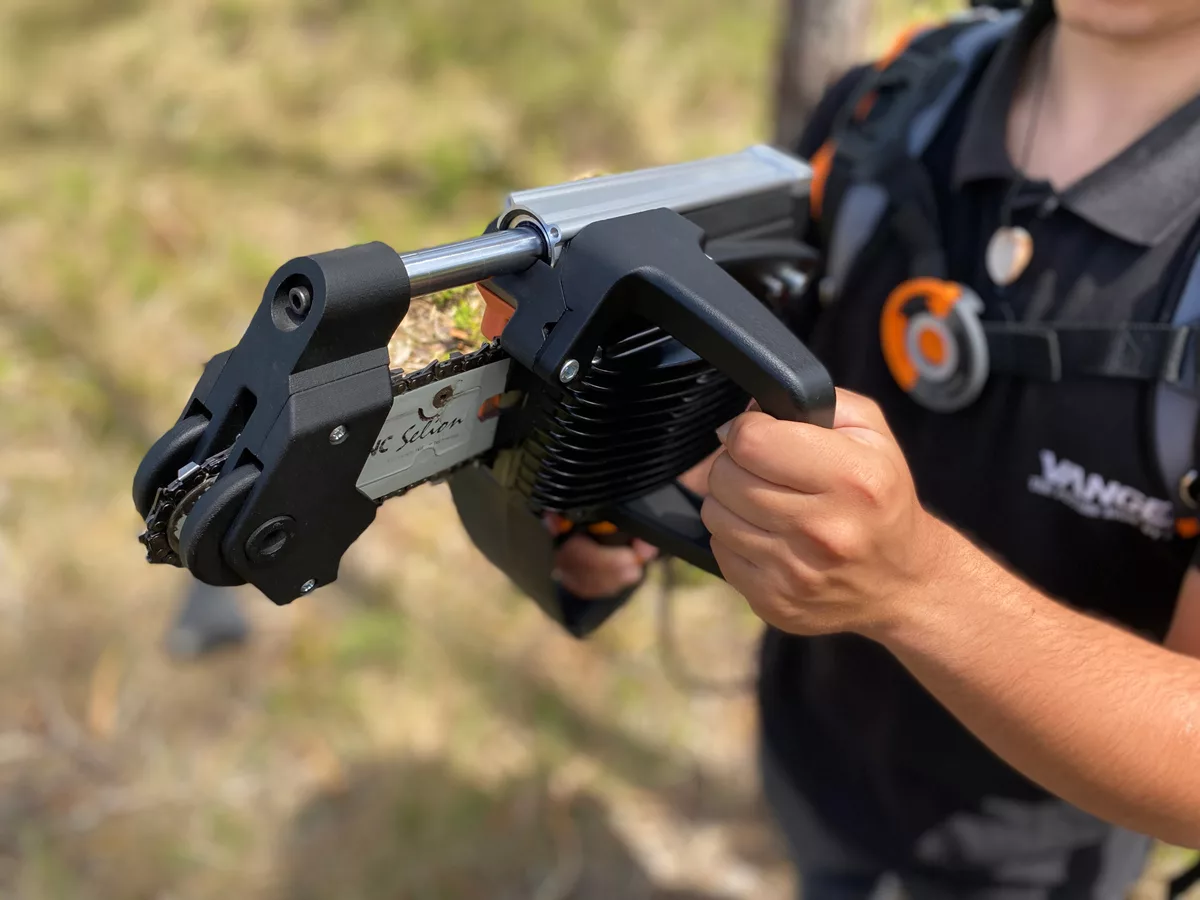
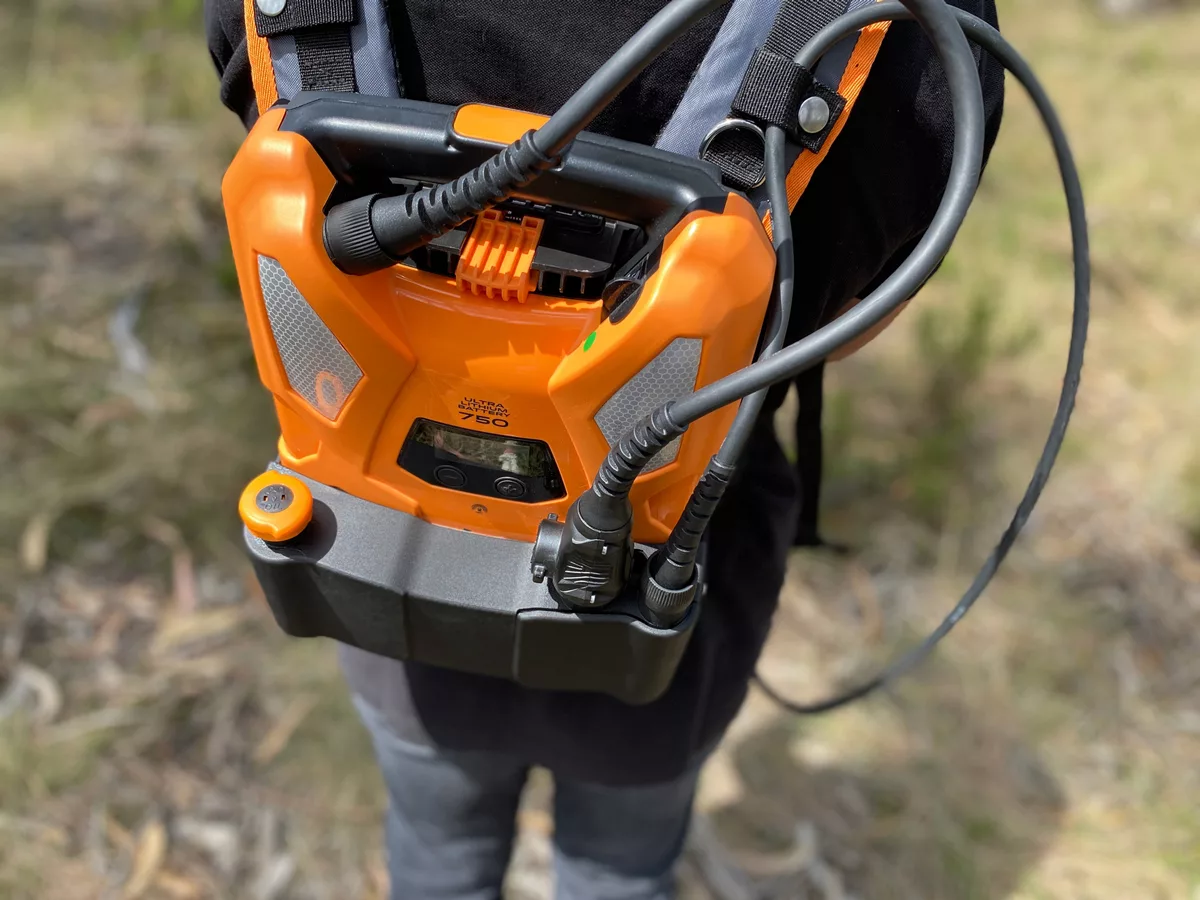
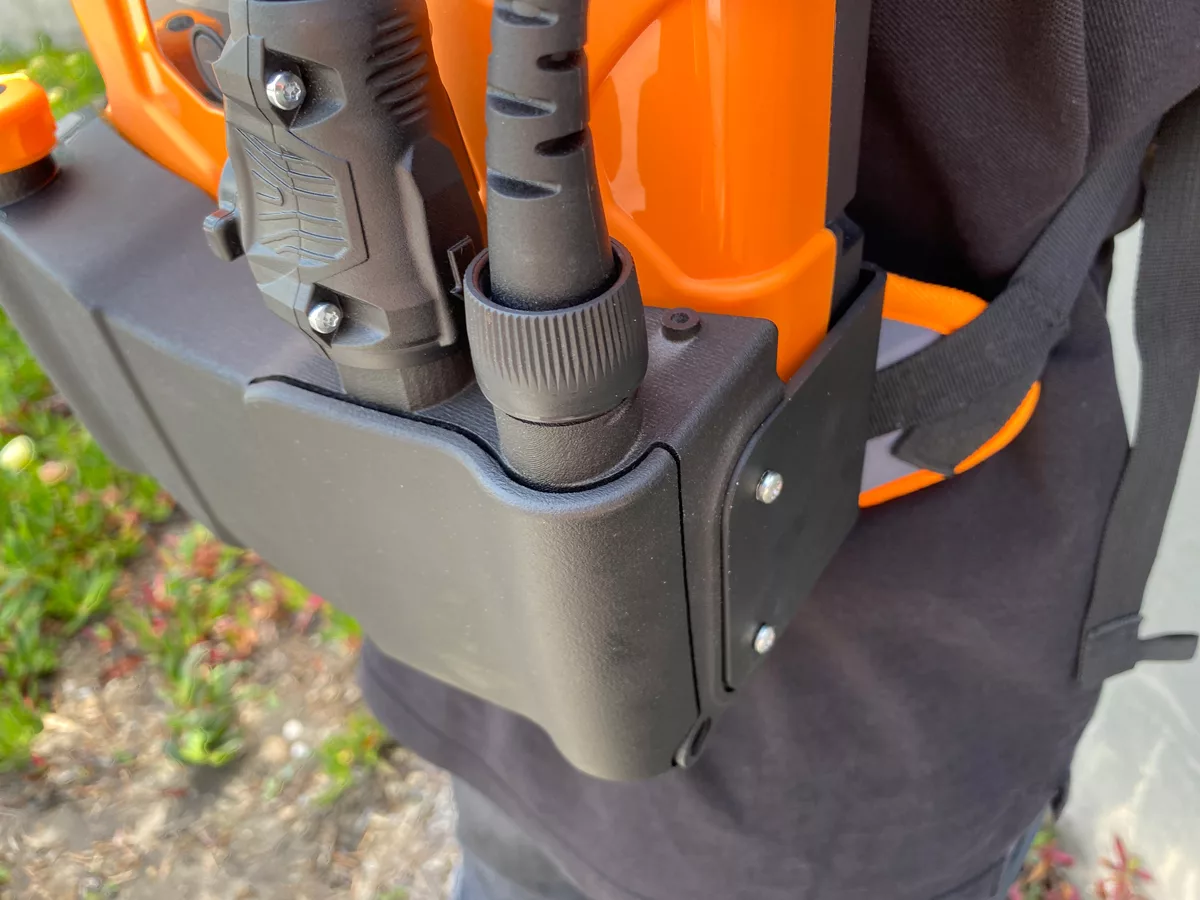